Preparation method of high-load modified silica gel dehumidification rotary core
A high-load, modified technology, applied in separation methods, chemical instruments and methods, silicon compounds, etc., can solve problems affecting adsorption performance and strength, and achieve increased silica gel loading, low desorption temperature, water absorption rate and The effect of increasing the saturated adsorption capacity
- Summary
- Abstract
- Description
- Claims
- Application Information
AI Technical Summary
Problems solved by technology
Method used
Image
Examples
preparation example Construction
[0034] A method for preparing a modified silica gel desiccant rotor core with a high loading capacity, comprising the following steps:
[0035] S1: drying and purging the sample block of the dehumidification rotor core, and then immersing in water glass and then purging with hot air. The concentration of water glass is 25%-35%. In a preferred embodiment, the concentration of the water glass is 30%.
[0036] The drying is at 100-120° C. for 20-30 min, and the purging is at a wind speed of 0.5-2 m / s for 10-15 min. In a preferred embodiment, the wind speed is 1 m / s.
[0037] In a preferred embodiment, the immersion is repeated pulling and immersion for 10-15 minutes.
[0038] The hot air blowing is carried out at 30-40° C. with hot air of 0.5-2 m / s for 0.5-2 hours. In a preferred embodiment, the wind speed is 1 m / s, and the hot air blowing time is 1 hour.
[0039] S2: Repeatedly and evenly spray the remaining water glass in step (1) onto the sample block obtained in step (1), ...
Embodiment 1
[0048] S1: Dry the dehumidified core glass fiber sample block at 100°C for 20 minutes, blow it with a wind speed of 1m / s for 10 minutes, and then soak it in water glass with a concentration of 25% at room temperature. After repeated pulling and dipping for 10 minutes, use 30 ℃, 1m / s hot air blowing for 1h;
[0049] S2: Spray the remaining water glass in step S1 on the sample block obtained in step S1, repeatedly and uniformly spray for 10 minutes, and blow with hot air at 30°C and 1 m / s for 2 hours.
[0050] S3: Select zinc sulfate to prepare a 10% aqueous solution, and dip the sample block obtained in step S2 in the solution in a 60°C water bath. During the reaction, use concentrated sulfuric acid to adjust the pH back to pH=1.0, dip for 1 hour, and react for 5 minutes each time Make a callback;
[0051] S4: Rinse the sample block reacted in step S3 until it is neutral with deionized water, and roast and dry at 100° C. to obtain a high loading rate dehumidification core samp...
Embodiment 2
[0054] S1: Dry the dehumidified core glass fiber sample block at 110°C for 20 minutes, blow it with a wind speed of 1m / s for 15 minutes, and then soak it in water glass with a concentration of 35% at room temperature. After repeated pulling and dipping for 15 minutes, use 40 ℃, 0.5m / s hot air blowing for 2h;
[0055] S2: Spray the remaining water glass in step S1 on the sample block obtained in step S1, repeatedly and uniformly spray for 15 minutes, and blow with hot air at 40°C and 0.5 m / s for 2 hours.
[0056] S3: Select zinc sulfate to prepare a 15% aqueous solution, and dip the sample block obtained in step S2 in the solution in a 65°C water bath. During the reaction, use concentrated sulfuric acid to adjust the pH back to pH=1.2, dip for 1 hour, and react for 5 minutes each time Make a callback;
[0057] S4: Rinse the sample blocks reacted in step S3 until neutral with deionized water, and bake and dry at 120° C. to obtain high-loading dehumidification core sample blocks...
PUM
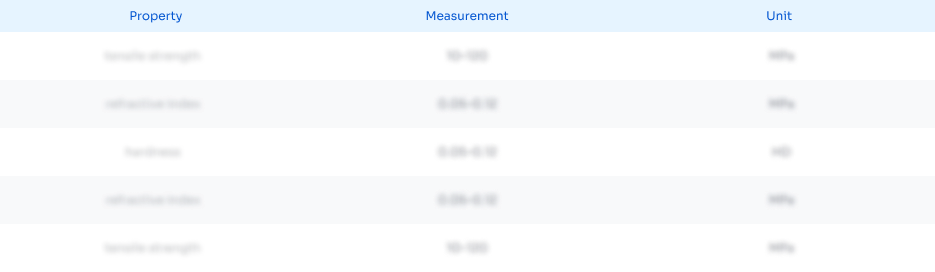
Abstract
Description
Claims
Application Information

- R&D
- Intellectual Property
- Life Sciences
- Materials
- Tech Scout
- Unparalleled Data Quality
- Higher Quality Content
- 60% Fewer Hallucinations
Browse by: Latest US Patents, China's latest patents, Technical Efficacy Thesaurus, Application Domain, Technology Topic, Popular Technical Reports.
© 2025 PatSnap. All rights reserved.Legal|Privacy policy|Modern Slavery Act Transparency Statement|Sitemap|About US| Contact US: help@patsnap.com