Forging method of Nb47Ti alloy large-size bar for superconducting wire
A superconducting wire, large-scale technology, used in manufacturing tools, metal processing equipment, forging/pressing/hammer devices, etc., can solve the problems of excessive forging times and increased costs, and achieve shortened forging times. The effect of uniform and small, cost reduction
- Summary
- Abstract
- Description
- Claims
- Application Information
AI Technical Summary
Problems solved by technology
Method used
Image
Examples
Embodiment 1
[0037] Step 1, blank forging:
[0038] Carry out the first fire forging of the Nb47Ti alloy ingot, the heating temperature of the first fire forging is 1160°C, and the heating time is 10h before it is released from the furnace, and the ingot is first upset and elongated, and the forging ratio is controlled at 1.4; then Carry out the second and third times of upsetting and elongating the ingot, the forging ratio is controlled at 1.7, and cooling is carried out after forging;
[0039] Step 2, intermediate forging:
[0040] The Nb47Ti alloy ingot after the billet forging in step 1 is subjected to the second fire forging. The heating temperature of the second fire forging is 980°C. After cooling;
[0041] Step 3, Finished Forging:
[0042] The Nb47Ti alloy ingot after the intermediate forging in step 2 is forged for the third fire with a radial forging machine, the heating temperature is 900°C, the forging ratio of the third fire forging is controlled at 4.0, and the radial for...
Embodiment 2
[0044] Step 1, blank forging:
[0045] The first fire forging is carried out on the Nb47Ti alloy ingot. The heating temperature of the first fire forging is 1200°C, and the heating time is 12 hours. Carry out the second and third times of upsetting and elongating the ingot, the forging ratio is controlled at 1.5, and cooling is carried out after forging;
[0046] Step 2, intermediate forging:
[0047] The Nb47Ti alloy ingot after the billet forging in step 1 is subjected to the second fire forging. The heating temperature of the second fire forging is 950°C. After cooling;
[0048] Step 3, Finished Forging:
[0049] The Nb47Ti alloy ingot after the intermediate forging in step 2 is forged with a radial forging machine for the third fire, the heating temperature is 870°C, the forging ratio of the third fire forging is controlled at 3.6, and the radial forging includes 4 deformation passes , the amount of deformation in each pass is 1.1, 1.4, 1.8, 1.3, and after forging, it ...
PUM
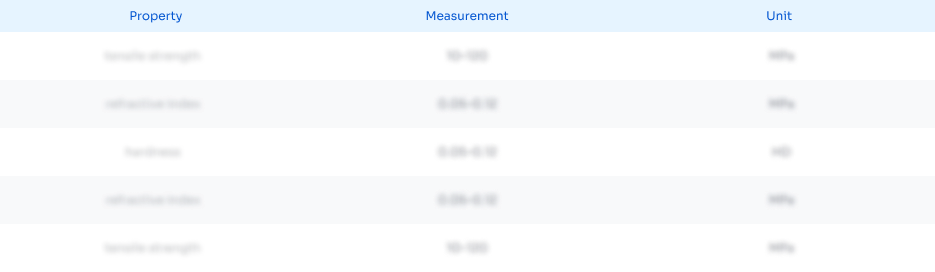
Abstract
Description
Claims
Application Information

- R&D
- Intellectual Property
- Life Sciences
- Materials
- Tech Scout
- Unparalleled Data Quality
- Higher Quality Content
- 60% Fewer Hallucinations
Browse by: Latest US Patents, China's latest patents, Technical Efficacy Thesaurus, Application Domain, Technology Topic, Popular Technical Reports.
© 2025 PatSnap. All rights reserved.Legal|Privacy policy|Modern Slavery Act Transparency Statement|Sitemap|About US| Contact US: help@patsnap.com