Laminated core assembly process method
A process method and core assembly technology, which is applied in the field of metal mold casting, can solve problems such as low production efficiency, poor sand core stability, and low positioning accuracy, and achieve high core assembly efficiency, reduce error accumulation, and ensure accuracy requirements.
- Summary
- Abstract
- Description
- Claims
- Application Information
AI Technical Summary
Problems solved by technology
Method used
Image
Examples
Embodiment Construction
[0077] In metal mold casting technology, the mold is used to form the appearance shape of the part, and the sand core is used to form the inner cavity shape of the part. Generally, the sand core needs to be installed on the mold, and the matching accuracy of the two must be high to produce the shape and size. Parts that meet the requirements of the product drawing. In order to improve precise positioning, the present invention designs a reference sand core to assist positioning, so as to realize high-precision matching and meet production requirements.
[0078] Specifically, core assembly is realized through the following process:
[0079] Step 1. Prepare the reference core and each sub-sand core;
[0080] Step 1.1. Design the reference core structure and sand core structure according to the casting inner cavity structure, sand core mold opening requirements, ejection requirements, core assembly operation, etc. This step can be realized by using existing conventional methods....
PUM
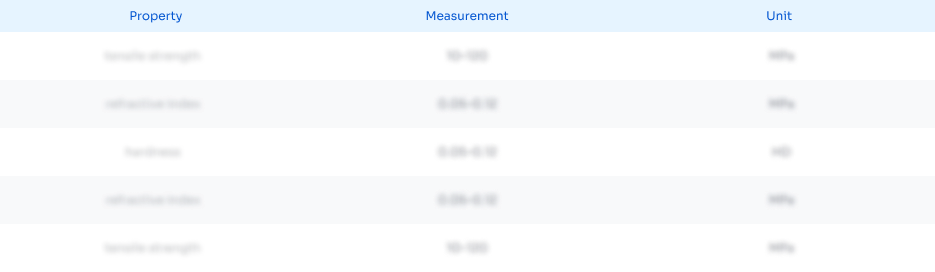
Abstract
Description
Claims
Application Information

- R&D Engineer
- R&D Manager
- IP Professional
- Industry Leading Data Capabilities
- Powerful AI technology
- Patent DNA Extraction
Browse by: Latest US Patents, China's latest patents, Technical Efficacy Thesaurus, Application Domain, Technology Topic, Popular Technical Reports.
© 2024 PatSnap. All rights reserved.Legal|Privacy policy|Modern Slavery Act Transparency Statement|Sitemap|About US| Contact US: help@patsnap.com