Highway tunnel intelligent inspection robot system based on multi-dimensional sensing
A technology for inspection robots and road tunnels, applied in general control systems, control/regulation systems, registration/indicating machines, etc., can solve problems such as deterioration of the tunnel environment, short disaster-causing time, failure of tunnel monitoring facilities, etc., to achieve Low labor intensity, simple and reliable structure, and high inspection efficiency
- Summary
- Abstract
- Description
- Claims
- Application Information
AI Technical Summary
Problems solved by technology
Method used
Image
Examples
Embodiment 1
[0070] Such as Figure 1 to Figure 4 As shown, the present invention discloses a multi-dimensional sensor-based intelligent inspection robot system for road tunnels, including:
[0071] The mobile robot subsystem can drive the multi-dimensional sensing subsystem to move in the inspected tunnel 1;
[0072] The multi-dimensional sensing subsystem can detect and obtain the equipment status data, tunnel environment data, and traffic condition data of the inspected tunnel 1;
[0073] The monitoring and management subsystem can receive the equipment status data, tunnel environment data, and traffic condition data in real time, and can analyze the Equipment failures, tunnel environment abnormalities, and traffic accidents in the inspected tunnel 1.
[0074] Therefore, the present invention can replace manual operation and maintenance inspection work of highway tunnels to detect abnormalities in time, and has the advantages of high reliability of inspection data, good standardizatio...
Embodiment approach
[0077] The mobile robot subsystem includes a running track 2 and an inspection robot 3. The running track 2 is installed on the top of the inspected tunnel 1 and extends along the direction of the inspected tunnel 1. The inspection robot 3 includes a track carrier 3-1, a lifting platform 3-2 and an installation body 3-3, the track carrier 3-1 is installed on the running track 2 and can run forward and backward along the running track 2, the The installation body 3-3 is installed on the track carrier 3-1 through the lifting platform 3-2, and the lifting platform 3-2 can drive the installation body 3-3 to move up and down;
[0078] Moreover, the multi-dimensional sensing subsystem is installed on the installation body 3-3, and the installation body 3-3 is also equipped with a control module, a positioning module, a communication module, and a robot for inspection. 3 power supply modules, the control modules are electrically connected to the control terminals of the track carrier...
Embodiment 3
[0086] On the basis of the above-mentioned embodiment 1 or embodiment 2, this embodiment 3 also adopts the following preferred implementation modes:
[0087] The multi-dimensional sensing subsystem includes an infrared thermal imaging camera, a brightness detector, and a wind speed and direction sensor; the device status data includes: the infrared thermal imaging camera detects the heating of the lighting equipment obtained from the lighting equipment in the inspected tunnel 1 temperature data; the brightness detector detects the illuminance data obtained from the lighting equipment in the inspected tunnel 1; the infrared thermal imaging camera detects the heat generated by the power supply and distribution equipment in the inspected tunnel 1 Temperature data; the wind speed and direction sensor detects the wind speed data obtained by the ventilation equipment in the inspected tunnel 1;
[0088] Thereby, the present invention can carry out inspection of tunnel facilities and ...
PUM
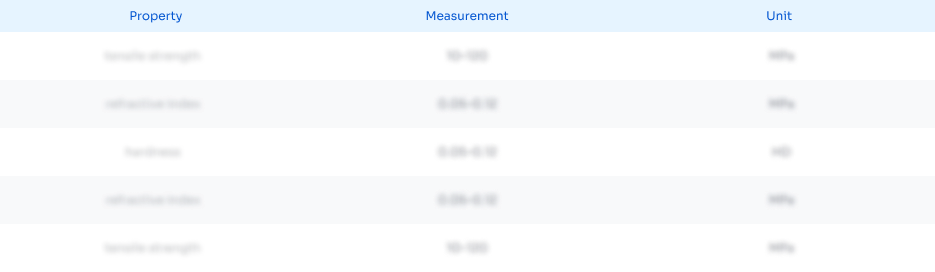
Abstract
Description
Claims
Application Information

- R&D Engineer
- R&D Manager
- IP Professional
- Industry Leading Data Capabilities
- Powerful AI technology
- Patent DNA Extraction
Browse by: Latest US Patents, China's latest patents, Technical Efficacy Thesaurus, Application Domain, Technology Topic, Popular Technical Reports.
© 2024 PatSnap. All rights reserved.Legal|Privacy policy|Modern Slavery Act Transparency Statement|Sitemap|About US| Contact US: help@patsnap.com