Cooling liquid recovery process for six-axis grinding machine
A cooling fluid and grinding machine technology, applied in manufacturing tools, metal processing equipment, grinding/polishing equipment, etc., can solve the problems of inability to discharge iron filings and grinding stone particles, increase the difficulty of filtration, and be impossible to achieve, so as to improve the use of water circulation. effect, increase the difficulty of filtering, and improve the effect of utilization
- Summary
- Abstract
- Description
- Claims
- Application Information
AI Technical Summary
Problems solved by technology
Method used
Image
Examples
Embodiment 1
[0058] Such as figure 1 As shown, a coolant recovery process for a six-axis grinder includes a workpiece grinding process, a cooling process, and an impurity screening process, and the impurity screening process includes:
[0059] Step 1, the wastewater is collected, the grinding mechanism 2 drives the impurity removal mechanism 5 to work through the first transmission mechanism 8, when any support shaft 52 moves towards the support plate 42, the other support shaft 52 moves away from the support plate 42, and then the support plate Impurities on the 42 are blown into the installation chamber 51 moving away from the support plate 42 along the airflow direction, that is, the impurities entering the installation chamber 51 are also subjected to the blowing force while being attracted, and the impurities are accelerated to enter the installation chamber 51 The speed, then the impurities entering the installation chamber 51 enter the discharge chute 503 along the discharge part 50...
Embodiment 2
[0077] Such as figure 2 As shown, a water cooling machine for a round table surface grinder includes a grinder 101, a grinding mechanism 2 installed on the grinder 101, a cooling mechanism 3 arranged on one side of the grinding mechanism 2, and a cooling mechanism 3 arranged below the grinding mechanism 2. And the carrying mechanism 4 installed on the grinding machine 101, two sets of impurity removal mechanisms 5 arranged symmetrically on both sides of the carrying mechanism 4 and used to collect impurities on the carrying mechanism 4, arranged on the An iron filings filter mechanism 6 arranged under the impurity removal mechanism 5 and communicated with the impurity removal mechanism 5 , and a grindstone particle filter mechanism 7 arranged under the iron filings filter mechanism 6 and communicated with the cooling mechanism 3 at the other end;
[0078]The impurity removal mechanism 5 works synchronously with the grinding mechanism 2 through the first transmission mechanism...
PUM
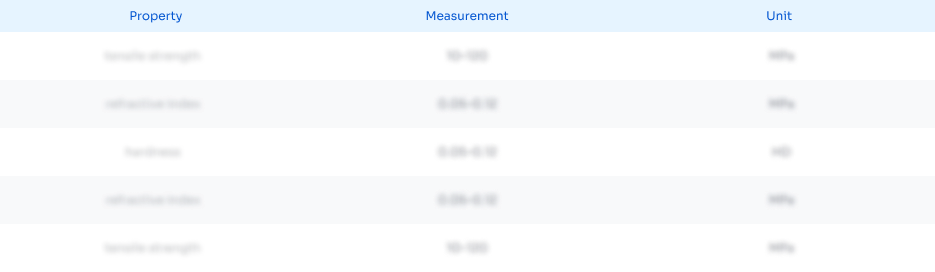
Abstract
Description
Claims
Application Information

- R&D
- Intellectual Property
- Life Sciences
- Materials
- Tech Scout
- Unparalleled Data Quality
- Higher Quality Content
- 60% Fewer Hallucinations
Browse by: Latest US Patents, China's latest patents, Technical Efficacy Thesaurus, Application Domain, Technology Topic, Popular Technical Reports.
© 2025 PatSnap. All rights reserved.Legal|Privacy policy|Modern Slavery Act Transparency Statement|Sitemap|About US| Contact US: help@patsnap.com