Rotary motor rotor and motor
A technology for rotating motors and rotors, applied to synchronous machines, electric components, electrical components, etc., can solve the problems of reduced motor output torque, unreduced load torque fluctuations, and reduced air gap magnetic density, etc., to achieve improved torque density and Torque value, widening the constant power operating range, and improving the effect of field weakening speed expansion ability
- Summary
- Abstract
- Description
- Claims
- Application Information
AI Technical Summary
Problems solved by technology
Method used
Image
Examples
Embodiment Construction
[0018] The technical solution of the present invention will be further described in detail below in conjunction with the accompanying drawings.
[0019] Such as Figure 1-2 As shown, a rotor for a rotating electric machine includes a rotor main body, six installation slots are evenly distributed around the radial outer side of the rotor main body, permanent magnets are arranged in the installation slots, and six radially outwardly convex arcs are arranged on the outer periphery of the rotor main body. surface and 12 grooves, the center of the arc surface is located on the radial inner side of the rotor body, the radius of the arc surface is smaller than the distance between the outer periphery of the rotor body and the center of the rotor body, and the rotor body is located on the outside of each pole permanent magnet. magnetic hole.
[0020] In order to achieve smaller rotor pole cutting, the radius of the arc surface is R1, the radial symmetry line of the arc surface passes...
PUM
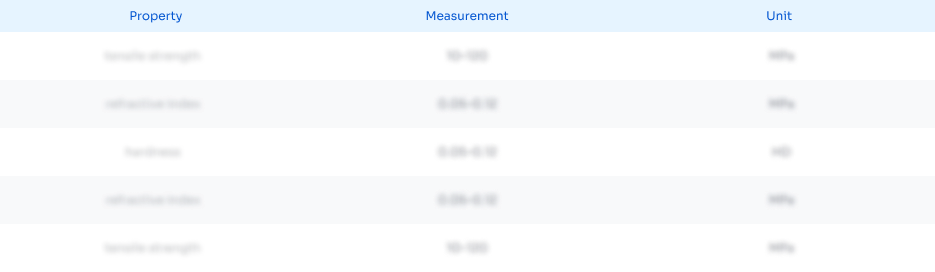
Abstract
Description
Claims
Application Information

- R&D Engineer
- R&D Manager
- IP Professional
- Industry Leading Data Capabilities
- Powerful AI technology
- Patent DNA Extraction
Browse by: Latest US Patents, China's latest patents, Technical Efficacy Thesaurus, Application Domain, Technology Topic, Popular Technical Reports.
© 2024 PatSnap. All rights reserved.Legal|Privacy policy|Modern Slavery Act Transparency Statement|Sitemap|About US| Contact US: help@patsnap.com