Automobile rear anti-collision beam connecting structure and rear anti-collision beam mounting method
A rear anti-collision beam and connection structure technology, applied to bumpers and other directions, can solve problems such as inconvenient glue application for workers, increased cost of rear floor molds, and complicated flanging molding, so as to avoid the risk of poor sealing, reduce weight and Cost, simple effect of flanging forming
- Summary
- Abstract
- Description
- Claims
- Application Information
AI Technical Summary
Problems solved by technology
Method used
Image
Examples
Embodiment
[0069]Figure 6 A schematic diagram of the post-collision beam connection structure of the present embodiment is shown;Figure 7 A sub-anti-collision beam connection structure exploded after the present embodiment is shown;Figure 8 showFigure 6 B-B profile;Figure 9A modification analysis of the post-collision beam connection structure of the present embodiment is shown.
[0070]Such asFigure 6 ,Figure 8 As shown, the rear collision beam connection structure includes: one side of the end plate reinforcing plate 2 is connected to the end of the rear beam 1, and the rear lever end plate 3 is disposed on the end plate reinforcing plate 2, and the outer plate 10 The outer surface of 10 is connected by welding, and then the collision beam 5 is connected to the rear collision beam mounting plate 4 through the suction cartridge 8, and the anti-collision beam mounting plate 4 is provided with a through hole, and the through hole corresponds to the suction cartridge 8. After the collision beam mou...
PUM
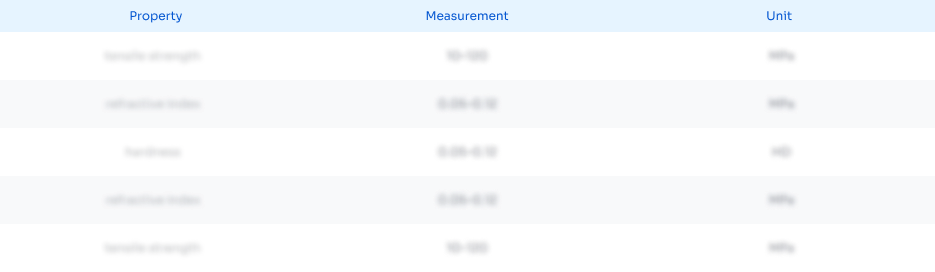
Abstract
Description
Claims
Application Information

- R&D Engineer
- R&D Manager
- IP Professional
- Industry Leading Data Capabilities
- Powerful AI technology
- Patent DNA Extraction
Browse by: Latest US Patents, China's latest patents, Technical Efficacy Thesaurus, Application Domain, Technology Topic, Popular Technical Reports.
© 2024 PatSnap. All rights reserved.Legal|Privacy policy|Modern Slavery Act Transparency Statement|Sitemap|About US| Contact US: help@patsnap.com