Comprehensive compensation method for position and attitude errors of industrial robot
An industrial robot, comprehensive compensation technology, applied in manipulators, manufacturing tools, program-controlled manipulators, etc., can solve the problems of uncompensated attitude errors, weak interpretability, small sampling point scale, etc., to expand application scenarios and improve processing. The effect of precision and accurate prediction
- Summary
- Abstract
- Description
- Claims
- Application Information
AI Technical Summary
Problems solved by technology
Method used
Image
Examples
Embodiment Construction
[0029] The following will clearly and completely describe the technical solutions in the embodiments of the present invention with reference to the accompanying drawings in the embodiments of the present invention. Obviously, the described embodiments are only some, not all, embodiments of the present invention. Based on the embodiments of the present invention, all other embodiments obtained by persons of ordinary skill in the art without creative efforts fall within the protection scope of the present invention.
[0030] see Figure 1-3 , the experimental platform of industrial robots includes industrial robots and their control cabinets, and binocular vision measurement devices. The end of the robot is equipped with an end effector. The industrial robot is a 6-degree-of-freedom open-chain manipulator. The repeatability of the robot is ±0.08mm. The robot moves the end effector to the target pose through the movement of the joints, but the end effector will deviate from the t...
PUM
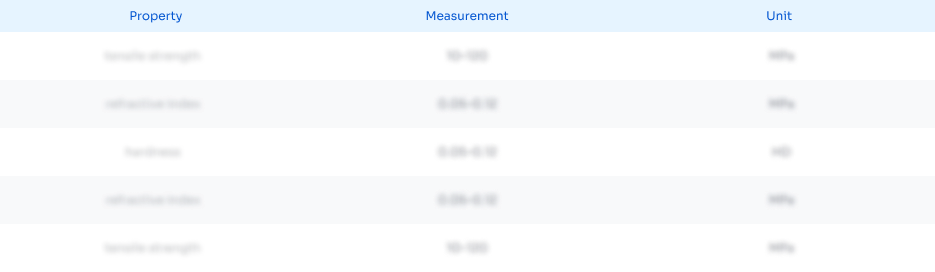
Abstract
Description
Claims
Application Information

- R&D
- Intellectual Property
- Life Sciences
- Materials
- Tech Scout
- Unparalleled Data Quality
- Higher Quality Content
- 60% Fewer Hallucinations
Browse by: Latest US Patents, China's latest patents, Technical Efficacy Thesaurus, Application Domain, Technology Topic, Popular Technical Reports.
© 2025 PatSnap. All rights reserved.Legal|Privacy policy|Modern Slavery Act Transparency Statement|Sitemap|About US| Contact US: help@patsnap.com