Mortise broaching process simulation analysis method based on heat-force-flow multi-field coupling
A technology of process simulation and analysis method, which is applied in design optimization/simulation, special data processing applications, instruments, etc. It can solve the problems of insufficient accuracy of simulation results, inability to accurately simulate the cooling and lubrication of workpieces and tools, and achieve the improvement of simulation accuracy Effect
- Summary
- Abstract
- Description
- Claims
- Application Information
AI Technical Summary
Problems solved by technology
Method used
Image
Examples
Embodiment 1
[0149] Example 1: Simulation optimization of broach rake angle
[0150] The material of the broach is M42 quenched + tempered high-speed steel, and the tongue and groove disc is made of GH4169 aging nickel-based superalloy material. The three-dimensional structure of the broach used for broaching is as follows: Figure 12 with Figure 13 shown. The parameters of the tool are: the relief angle is 3°, the radius of the blunt circle of the cutting edge is 0.02mm, the tooth lift is 0.03mm, and the broaching speed is 6m / min. The influence of the rake angle on the temperature distribution of broaching simulation is compared and analyzed. Carry out the broaching simulation of tools with rake angles of 6°, 10°, 15° and 18° respectively.
[0151] Repeat the simulation and tool parameter optimization steps of this embodiment to obtain the blade temperature distribution and broaching force simulation results with different rake angle parameters, such as Figure 14 shown. It can be se...
Embodiment 2
[0154] Embodiment 2: Simulation optimization of blunt circle radius of broach blade
[0155] The material of the broach is ASP2015 powder metallurgy steel quenched + tempered material, and the tenon and groove disc is FGH95 aging nickel-based superalloy material. The three-dimensional structure of the broach used for broaching is as follows: Figure 16 with Figure 17 shown. The parameters of the tool are: the rake angle and the relief angle are 10° and 3° respectively, the broaching speed is 2m / min, the tooth lift is 0.03mm, and the broaching speed is 6m / min. Simulate the effect of temperature distribution. Carry out the broaching simulation of tools with blunt circle radii of 0.01mm, 0.02mm, 0.03mm and 0.04mm respectively.
[0156] Figure 18 It is a comparison chart of the influence of different cutting edge blunt circle radii on cutting stress (Misses Stress). It can be seen from the results that the stress decreases with the increase of the blunt circle radius. When...
Embodiment 3
[0159] Example 3: Simulation optimization of broach tooth lift
[0160] The material of the broach is M42 high-speed steel quenched and tempered, and the tongue and groove disc is made of FGH95 aging nickel-based superalloy material. The three-dimensional structure of the broach used for broaching is as follows: Figure 20 with Figure 21 shown. The rake angle and relief angle of the broach are 10° and 3°, respectively, and the broaching speed is 2m / min. Carry out broaching simulations of tools with tooth lifts of 0.02mm, 0.03mm, 0.04mm and 0.05mm respectively.
[0161] Figure 22 It is the simulation comparison result of the influence of different tooth lifts on the residual stress (X direction). It can be seen from the figure that the distribution area of residual stress gradually increases with the increase of tooth lift.
[0162] Figure 23 It is a schematic diagram of the change of cutting force in the X and Y directions with the tool tooth lift and time. From bot...
PUM
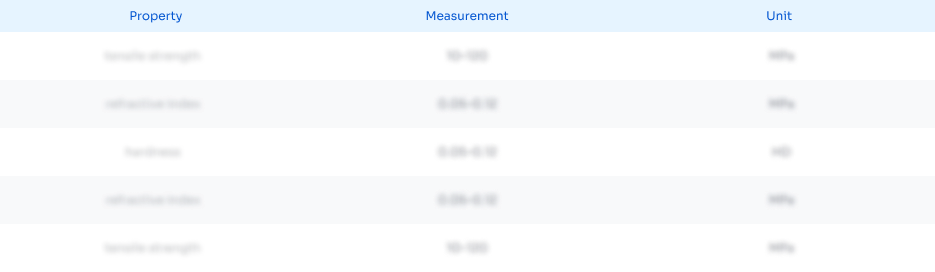
Abstract
Description
Claims
Application Information

- Generate Ideas
- Intellectual Property
- Life Sciences
- Materials
- Tech Scout
- Unparalleled Data Quality
- Higher Quality Content
- 60% Fewer Hallucinations
Browse by: Latest US Patents, China's latest patents, Technical Efficacy Thesaurus, Application Domain, Technology Topic, Popular Technical Reports.
© 2025 PatSnap. All rights reserved.Legal|Privacy policy|Modern Slavery Act Transparency Statement|Sitemap|About US| Contact US: help@patsnap.com