A Bending Mold for U-shaped Parts of Medium-thick Orifice Plate with Asymmetrical Channel Structure
A channel structure and bending forming technology, which is applied in the direction of forming tools, manufacturing tools, metal processing equipment, etc., can solve the problems of difficult manufacturing process of the first wall, achieve uniform deformation, avoid cracking, and ensure the effect of dimensional accuracy
- Summary
- Abstract
- Description
- Claims
- Application Information
AI Technical Summary
Problems solved by technology
Method used
Image
Examples
Embodiment
[0033] Such as figure 1 As shown, the present invention provides a kind of bending forming mold for medium-thick orifice plate U-shaped parts with asymmetric channel structure, including T-shaped force transmission part 1, bending pressure head 2, first rotatable support part 3, second rotatable support part 4 and the die 5; the die 5 is provided with a groove 6, one end of the die 5 is connected to the first rotatable support 3, and the other end of the second rotatable support 4 is connected to the second rotatable support 4 . Wherein, the first rotatable support member 3 and the second rotatable support member 4 are respectively provided with downward slideway grooves, and the lower end of the T-shaped force transmission member 1 is equipped with a bending indenter 2, and the bending indenter 2 and the groove 6 Matching, when the bending head 2 moves down to the groove 6 through the T-shaped force transmission part 1 through the groove of the down slideway, the medium-thic...
PUM
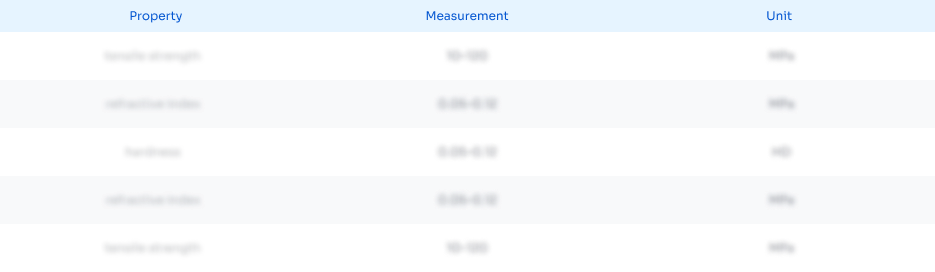
Abstract
Description
Claims
Application Information

- R&D Engineer
- R&D Manager
- IP Professional
- Industry Leading Data Capabilities
- Powerful AI technology
- Patent DNA Extraction
Browse by: Latest US Patents, China's latest patents, Technical Efficacy Thesaurus, Application Domain, Technology Topic, Popular Technical Reports.
© 2024 PatSnap. All rights reserved.Legal|Privacy policy|Modern Slavery Act Transparency Statement|Sitemap|About US| Contact US: help@patsnap.com