Three-channel pulverized coal burner and rotary kiln with same
A pulverized coal burner and three-channel technology are applied in the directions of burners, burners, and combustion methods for burning powder fuel, which can solve the problems of heating burden, increase in nitrogen oxides, and increase in fuel consumption, and achieve easy installation and good quality. Industrial production value, the effect of simple structure
- Summary
- Abstract
- Description
- Claims
- Application Information
AI Technical Summary
Problems solved by technology
Method used
Image
Examples
Embodiment 1
[0037] The coal feed rate of the rotary kiln is 5.2 t / h, the opening degree of the control disc valve I on the outer layer of the three-channel pulverized coal burner is 80%, the opening degree of the control disc valve II on the middle layer is 30%, and the opening degree of the control disc valve III on the inner layer is When the opening is 60%, the flame shape is regular, the length is 17±0.5 meters, and the temperature of the rotary kiln head is 1130±10°C.
Embodiment 2
[0039] The coal feed rate of the rotary kiln is 5.2 t / h, the opening degree of the control disc valve I on the outer layer of the three-channel pulverized coal burner is 100%, the opening degree of the control disc valve II on the middle layer is 0%, and the opening degree of the control disc valve III on the inner layer is When the opening is 80%, the flame shape is regular, the length is 19 ± 0.5 meters, and the temperature of the rotary kiln head is 1100 ± 10 °C.
Embodiment 3
[0041] The coal feed rate of the rotary kiln is 5.2 t / h, the opening degree of the control disc valve I on the outer layer of the three-channel pulverized coal burner is 60%, the opening degree of the control disc valve II on the middle layer is 100%, and the opening degree of the control disc valve III on the inner layer is When the opening is 20%, the flame shape is regular, the length is 15±0.5 meters, and the temperature of the rotary kiln head is 1150±10°C.
[0042] Adopt the method that above-mentioned embodiment provides and compare before adopting method and mainly have following effect:
[0043] (1) The flame shape and length can be adjusted in a wider range;
[0044] (2) Avoid local continuous high temperature in the kiln, so that the temperature in the rotary kiln is more uniform.
PUM
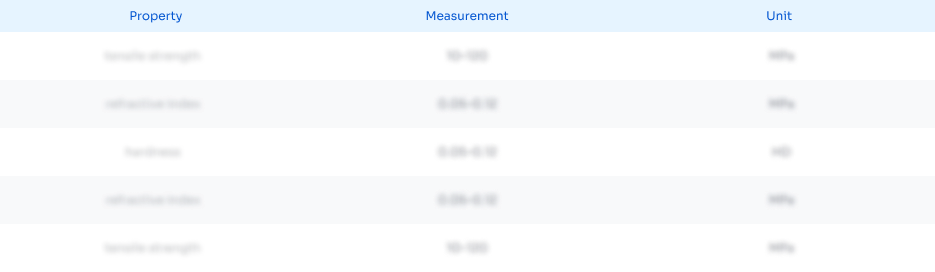
Abstract
Description
Claims
Application Information

- R&D
- Intellectual Property
- Life Sciences
- Materials
- Tech Scout
- Unparalleled Data Quality
- Higher Quality Content
- 60% Fewer Hallucinations
Browse by: Latest US Patents, China's latest patents, Technical Efficacy Thesaurus, Application Domain, Technology Topic, Popular Technical Reports.
© 2025 PatSnap. All rights reserved.Legal|Privacy policy|Modern Slavery Act Transparency Statement|Sitemap|About US| Contact US: help@patsnap.com