Automatic assembling system for steel wire thread insert
A technology for wire screw inserts and automatic assembly, which is applied in metal processing, metal processing equipment, manufacturing tools, etc., can solve the problems of low assembly efficiency, inability to realize automatic assembly, and high labor costs, so as to improve assembly efficiency, reduce labor costs, and reduce labor costs. The effect of reducing labor intensity
- Summary
- Abstract
- Description
- Claims
- Application Information
AI Technical Summary
Problems solved by technology
Method used
Image
Examples
Embodiment 1
[0038] The present invention provides an automatic assembly system for wire threaded sleeves, including an assembly device, an assembly line platform, a blocking device, a workpiece grabbing device, and a control device. The wire threaded sleeves in the present invention are also called wire sleeves, screw sleeves, and thread expansion sleeves. specifically:
[0039] The assembly device is used for grasping the workpiece to be assembled on the assembly platform, positioning the screw hole of the workpiece to be assembled and assembling the wire thread sleeve in the screw hole of the workpiece to be assembled.
[0040] Specifically, the assembly device adopts a four-axis mechanical transmission device, the four axes on the four-axis mechanical transmission device can be rotated at any angle, and the repeat positioning accuracy of the four-axis mechanical transmission device can reach ±0.02 mm, The four-axis mechanical transmission device can be programmed and controlled, and ha...
Embodiment 2
[0047] Embodiment 2 is a variation example of embodiment 1, specifically as follows:
[0048] The invention provides an automatic assembly system for wire threaded sleeves, which includes an assembly device, an assembly line platform, a blocking device, a workpiece grabbing device, a visual positioning system and a control device, the control device adopts a computer, and the workpiece grabbing device adopts a fixed effect combination The structure of the cylinder oil cylinder, when the workpiece to be assembled is grabbed from the assembly line platform to the assembly platform, the workpiece grabbing device will fix the workpiece to be assembled to the installation position on the assembly platform through the fixing pin, and then pass the two cylinders. The assembly workpiece is pressed tightly to ensure the stability of the workpiece to be assembled, and it is convenient to install the wire screw sleeve.
[0049] The control device is also provided with a voice control sys...
Embodiment 3
[0053] Embodiment 3 is a preferred example of embodiment 1:
[0054] The invention provides an automatic assembly system for wire thread inserts, which includes an assembly device, an assembly line platform, a blocking device, a workpiece grabbing device, and a control device. The assembly device includes an intelligent screwdriver, a special batch head for wire thread inserts, and a pressing device. When it is necessary to assemble the wire thread insert, the special bit for the wire thread insert grabs the wire thread insert and moves the wire thread insert to the position of the screw hole of the workpiece to be assembled, and the pressing device pushes the wire thread insert Press on the screw hole of the workpiece to be assembled and complete the assembly of the wire screw sleeve by the intelligent screwdriver. The torque of the intelligent screwdriver can reach up to 30-160mN.m, the torque accuracy is ±5%, and the detection accuracy is greater than Or equal to 0.01r.
...
PUM
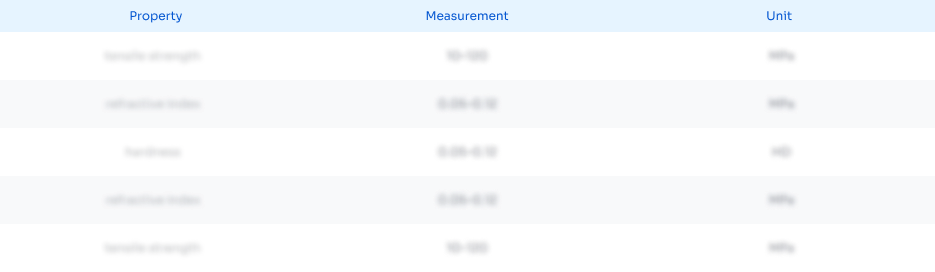
Abstract
Description
Claims
Application Information

- R&D
- Intellectual Property
- Life Sciences
- Materials
- Tech Scout
- Unparalleled Data Quality
- Higher Quality Content
- 60% Fewer Hallucinations
Browse by: Latest US Patents, China's latest patents, Technical Efficacy Thesaurus, Application Domain, Technology Topic, Popular Technical Reports.
© 2025 PatSnap. All rights reserved.Legal|Privacy policy|Modern Slavery Act Transparency Statement|Sitemap|About US| Contact US: help@patsnap.com