Machining device for outer profile of integral spinning type hemispherical shell
A technology of external surface and adding devices, which is applied in the direction of positioning devices, clamping devices, metal processing equipment, etc., can solve the problems of low machining efficiency of hemispherical shell heads, efficiency of hemispherical shell heads and product qualification rate Low, low accuracy of positioning and clamping to achieve the effect of ensuring product processing quality and processing accuracy stability, improving overall processing efficiency, and efficient and stable clamping
- Summary
- Abstract
- Description
- Claims
- Application Information
AI Technical Summary
Problems solved by technology
Method used
Image
Examples
Embodiment Construction
[0038] Below in conjunction with accompanying drawing and embodiment of description, specific embodiment of the present invention is described in further detail:
[0039] refer to Figure 4 to Figure 16 The shown one kind of integral spinning hemispherical shell outer surface machining device includes a positioning seat, a shape adjustment mechanism 3 and a pressing mechanism 2 arranged directly above the positioning seat. The positioning seat includes a self-downward The positioning carcass 1, the middle stand 11 and the welding base 12 of the hemispherical structure distributed in sequence, the pressing mechanism 2 includes a top pressing assembly and an outer pressing assembly, and the adjusting and correcting mechanism 3 includes a radial Adjusting mechanism and clamping and shaping mechanism, the top pressing assembly includes a top pressing plate 21 and a vertical bolt 22 threaded with the top of the positioning carcass 1, and the outer pressing assembly includes a The ...
PUM
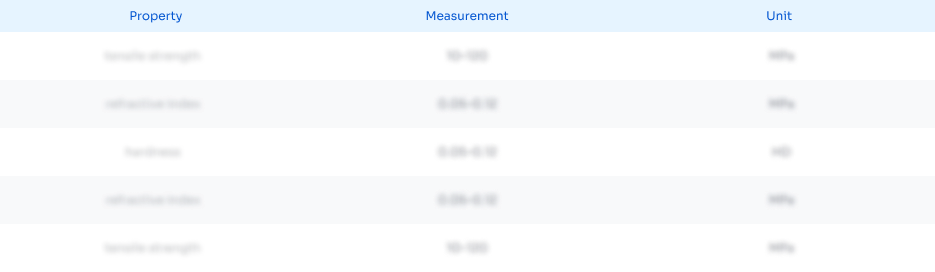
Abstract
Description
Claims
Application Information

- R&D Engineer
- R&D Manager
- IP Professional
- Industry Leading Data Capabilities
- Powerful AI technology
- Patent DNA Extraction
Browse by: Latest US Patents, China's latest patents, Technical Efficacy Thesaurus, Application Domain, Technology Topic, Popular Technical Reports.
© 2024 PatSnap. All rights reserved.Legal|Privacy policy|Modern Slavery Act Transparency Statement|Sitemap|About US| Contact US: help@patsnap.com