Process for improving SO2 desorption efficiency of desulfurization absorbent
An absorbent and SO2 technology, applied in the direction of gas treatment, membrane technology, dispersed particle separation, etc., can solve the problems of greatly increased steam consumption, increased operating costs, high failure rate, etc., to improve the secondary steam utilization rate, temperature and The effect of increasing the pressure and improving the desorption efficiency
- Summary
- Abstract
- Description
- Claims
- Application Information
AI Technical Summary
Problems solved by technology
Method used
Image
Examples
Embodiment 1
[0032] A polymetallic resource recycling plant, the flue gas volume ~ 600000Nm 3 / h, SO 2 Concentration 12~30g / Nm 3 , flue gas temperature ~ 80 ° C, flue gas pressure ~ 8.5KPa, using organic amine desulfurization combined with the double-tower double-effect + desorption low pressure variable load depth desorption process provided by the present invention, the desorption temperature in the high-pressure desorption tower 1 is 110 ~120℃, desorption pressure 130~190KPa, frequency conversion booster 5 pressurization 45~65KPa, pre-desorption temperature in low pressure desorption tower 3 105~110℃, pre-desorption pressure 135~150KPa, raw steam consumption 32t / h, flue gas exhaust SO 2 Concentration ~ 20 mg / m 3 , particle concentration ≤ 5 mg / m 3 , the system power consumption load is 2230KW, and the direct consumption cost is about 635 yuan / ton SO 2 , The device layout is simple and occupies less land, and the operation is simple, which achieves the purpose of saving investment ...
Embodiment 2
[0034] A waste lead battery resource recycling factory, the flue gas volume is 100000+200000Nm 3 / h, SO 2 Concentration 12~30g / Nm 3 , flue gas temperature ~ 80 ℃, flue gas pressure ~ 8.0KPa, using organic amine desulfurization combined with the double-tower double-effect + desorption low pressure variable load depth desorption process provided by the present invention, the desorption temperature in the high-pressure desorption tower 1 is 108 ~118℃, desorption pressure 130~175KPa, frequency conversion booster 5 pressurization 35~70KPa, pre-desorption temperature in low pressure desorption tower 3 103~109℃, pre-desorption pressure 120~145KPa, raw steam consumption 11.8 t / h, flue gas exhaust SO 2 Concentration ~ 20 mg / m 3 , particle concentration ≤ 5 mg / m 3 , the system power consumption load is 1130KW, and the direct consumption cost is about 680 yuan / ton SO 2, The arrangement of the device is simple, it occupies less land, the operation efficiency is high, and the manageme...
PUM
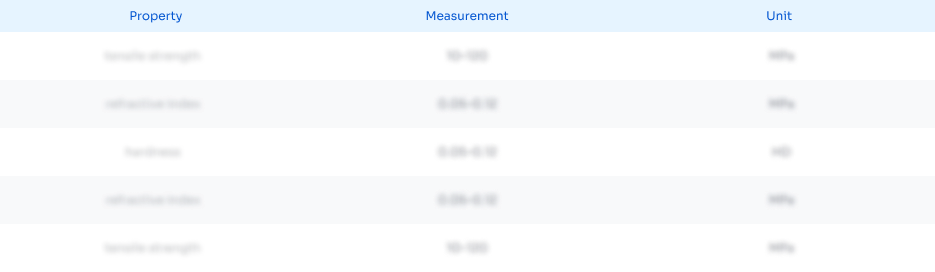
Abstract
Description
Claims
Application Information

- Generate Ideas
- Intellectual Property
- Life Sciences
- Materials
- Tech Scout
- Unparalleled Data Quality
- Higher Quality Content
- 60% Fewer Hallucinations
Browse by: Latest US Patents, China's latest patents, Technical Efficacy Thesaurus, Application Domain, Technology Topic, Popular Technical Reports.
© 2025 PatSnap. All rights reserved.Legal|Privacy policy|Modern Slavery Act Transparency Statement|Sitemap|About US| Contact US: help@patsnap.com