Bearing test result evaluation method
A technology of result evaluation and bearing test, which is applied in the direction of mechanical bearing test, mechanical component test, machine/structural component test, etc., can solve the problems that cannot meet the assessment requirements of aviation bearing test, and there is no evaluation method of bearing test result, etc., to achieve The effect of speeding up the process of localization substitution and complete standard content
- Summary
- Abstract
- Description
- Claims
- Application Information
AI Technical Summary
Problems solved by technology
Method used
Image
Examples
specific Embodiment approach 1
[0034] Specific Embodiment 1: In this embodiment, a bearing test result evaluation method includes steps before the test, steps during the test and steps after the test;
[0035] Step 1: The steps before the test include:
[0036] Step 11: test bearing inspection;
[0037] Step 1 and 2: Test equipment inspection;
[0038] Step 13: Installation and debugging;
[0039] Step 2: The steps in the test include:
[0040] Step 21: During the test, monitor the bearing speed, load, temperature, oil supply pressure, oil inlet and outlet temperature, and vibration of the main body of the testing machine;
[0041] Step 2 and 2: The test personnel conduct inspections and records according to the regulations, do a good job in equipment inspection and maintenance, and ensure that the equipment systems are in good condition;
[0042] Step 2 and 3: If any abnormality is found in the test, stop the machine for inspection, find out the cause or dismantle the machine to check the bearing, and ...
specific Embodiment approach 2
[0063] Specific implementation mode 2: The difference between this implementation mode and specific implementation mode 1 is: the standard for checking the test bearing in step 11 is: ①, the state of the test bearing should be consistent with the bearing pattern; ②, the quality certification documents of the test bearing should be complete, and Consistent with the real thing; ③. The test bearing is clean in appearance, free of scratches, bruises and corrosion. Other steps are the same as in the first embodiment.
specific Embodiment approach 3
[0064] Specific implementation mode three: the difference between this implementation mode and specific implementation mode one or two is: the standard for checking the test equipment in step one or two is: 1. The test equipment should be checked and accepted by appraisal, and regular maintenance and maintenance should be carried out to ensure The test equipment is in good condition; ②, the measuring equipment used for the test should be verified or calibrated, meet the test requirements, and be within the validity period; ③, whether the speed, load, oil supply temperature and oil supply pressure control accuracy of the test equipment meet the requirements, that is, the requirements The speed error is not greater than ±1%F.S, the load error is not greater than ±2%F.S, the oil supply temperature error is not greater than ±2%F.S, and the oil supply pressure error is not greater than ±5%F.S. Other steps are the same as those in Embodiment 1 or 2.
PUM
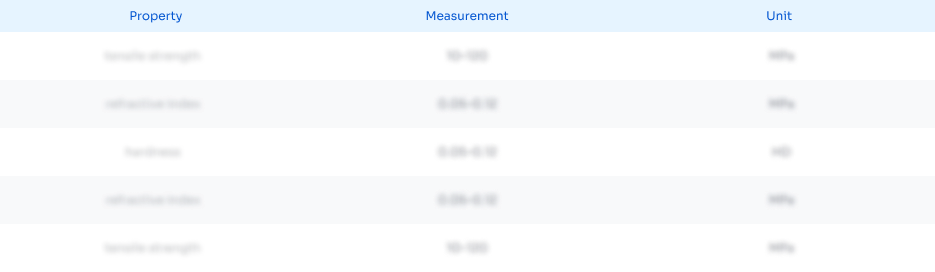
Abstract
Description
Claims
Application Information

- R&D Engineer
- R&D Manager
- IP Professional
- Industry Leading Data Capabilities
- Powerful AI technology
- Patent DNA Extraction
Browse by: Latest US Patents, China's latest patents, Technical Efficacy Thesaurus, Application Domain, Technology Topic, Popular Technical Reports.
© 2024 PatSnap. All rights reserved.Legal|Privacy policy|Modern Slavery Act Transparency Statement|Sitemap|About US| Contact US: help@patsnap.com