Continuous reaction production method of maleic anhydride grafted chlorinated polyethylene copolymer rubber
A technology of chlorinated polyethylene and maleic anhydride, which is applied in the field of continuous reaction production of maleic anhydride grafted chlorinated polyethylene copolymer rubber, which can solve the problems of wear resistance, self-bonding and bonding with reinforcing fabrics or steel wires Problems such as poor performance, large product shrinkage, and easy tearing of the product can achieve the effects of temperature control, increased contact area, and short residual time
- Summary
- Abstract
- Description
- Claims
- Application Information
AI Technical Summary
Problems solved by technology
Method used
Image
Examples
Embodiment 1
[0029] This embodiment provides a continuous reaction production method of maleic anhydride grafted chlorinated polyethylene copolymer rubber, the specific steps are:
[0030] 1. choose weight-average molecular weight (Mw) to be 100,000, chlorine weight percentage content is 20Kg of chlorinated polyethylene rubber CM powder 20Kg of 35%, acid absorbing agent highly active magnesium oxide 0.2kg, stabilizer calcium stearate 0.3kg, anti- Oxygen agent 1010 is 0.1kg, after the above-mentioned materials are mixed uniformly, drop into the barrel of metering in the twin-screw continuous reactor band of the same direction;
[0031] 2. Weigh 0.6kg of maleic anhydride, dissolve it in 0.09kg of acetone, and pour the dissolved solution into the sealed barrel of the co-rotating twin-screw continuous reactor with metering;
[0032] 3. Weigh 0.1kg of tert-butyl peroxypivalate, dissolve it in 0.02kg of acetone, and pour the dissolved solution into a sealed cylinder with metering in a co-rotatin...
Embodiment 2
[0039] This embodiment provides a continuous reaction production method of maleic anhydride grafted chlorinated polyethylene copolymer rubber, the specific steps are:
[0040] 1. choose weight-average molecular weight (Mw) to be 150,000, chlorine weight percent content is 20Kg of chlorinated polyethylene rubber CM powder 20Kg of 32%, acid absorbing agent hydrotalcite 0.3kg, organotin stabilizer 0.5kg, antioxidant 168 is 0.15kg, after mixing the above materials evenly, put them into the barrel of the co-rotating twin-screw continuous reactor with metering;
[0041] 2. Weigh 0.5kg of maleic anhydride, dissolve it in 0.10kg of acetone, and pour the dissolved solution into the sealed barrel of the co-rotating twin-screw continuous reactor with metering;
[0042] 3. Weigh 0.06kg of tert-butyl peroxide-3,5,5-trimethylacetate, dissolve it in 0.012kg of acetone, and pour the dissolved solution into a co-rotating twin-screw continuous reactor with metering closed in the barrel;
[00...
Embodiment 3
[0049] This embodiment provides a continuous reaction production method of maleic anhydride grafted chlorinated polyethylene copolymer rubber, the specific steps are:
[0050] 2. Choose weight average molecular weight (Mw) as 180,000, chlorine weight percent content is 20Kg of chlorinated polyethylene rubber CM powder 20Kg of 40%, acid absorbing agent high active magnesium hydroxide 0.6kg, rare earth stabilizer 0.3kg, antioxidant 1076 is 0.06kg, after above-mentioned material is mixed, drop in the barrel of metering of co-rotating twin-screw continuous reactor band;
[0051] 2. Weigh 0.8kg of maleic anhydride, dissolve it in 0.12kg of acetone, and pour the dissolved solution into the sealed barrel of the co-rotating twin-screw continuous reactor with metering;
[0052]3. Weigh 0.08kg of dilauroyl peroxide, dissolve it in 0.016kg of acetone, and pour the dissolved solution into a parallel twin-screw continuous reactor with a metered closed barrel;
[0053] 4. The temperature o...
PUM
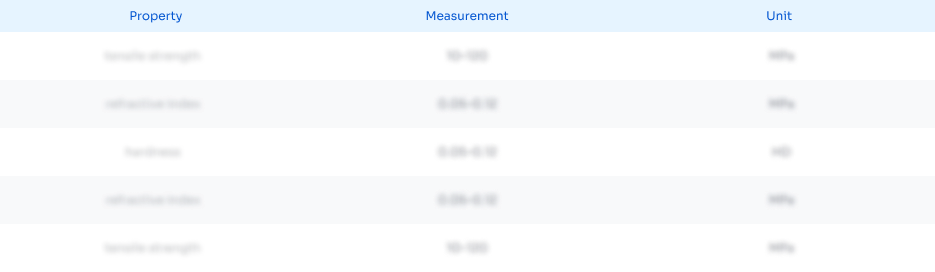
Abstract
Description
Claims
Application Information

- Generate Ideas
- Intellectual Property
- Life Sciences
- Materials
- Tech Scout
- Unparalleled Data Quality
- Higher Quality Content
- 60% Fewer Hallucinations
Browse by: Latest US Patents, China's latest patents, Technical Efficacy Thesaurus, Application Domain, Technology Topic, Popular Technical Reports.
© 2025 PatSnap. All rights reserved.Legal|Privacy policy|Modern Slavery Act Transparency Statement|Sitemap|About US| Contact US: help@patsnap.com