Combustion drag reduction method and device applied to scramjet engine
A scramjet and engine technology, applied in ramjet engines, combustion methods, engine components, etc., can solve the problems of fuel flameout in the engine, affecting the normal use of the engine, etc., to reduce frictional resistance and reduce frictional resistance. Effect
- Summary
- Abstract
- Description
- Claims
- Application Information
AI Technical Summary
Problems solved by technology
Method used
Image
Examples
Embodiment 1
[0026] see Figure 1-4 , a combustion drag reduction method applied to scramjet engines, injecting gaseous hydrogen fuel into the concave cavity 2 of the scramjet flame stabilizer 1, using the spark plug 5 to realize forced ignition, so that the fuel can be burned stably; the fuel combustion changes The flow structure of the scramjet reduces the velocity near the wall of the scramjet, thereby reducing the velocity gradient near the wall of the scramjet and reducing the frictional resistance of the scramjet.
[0027] This embodiment is different from the traditional combustion drag reduction mechanism. The flow structure of the scramjet is changed by combustion, and the velocity gradient near the engine wall is reduced, thereby reducing the frictional resistance of the engine. The invention will change the current common understanding on the mechanism of combustion drag reduction, and enrich and perfect the mechanism of combustion drag reduction. However, the drag-reducing met...
Embodiment 2
[0032] In this embodiment, the engine model such as figure 1 As shown, the inlet interface of the isolation section of the engine model is 30mm×150mm, the overall length of the model is 1073mm, the size of the fuel injection block 3 is 140mm×80mm×60mm, the cavity 2 is 11mm deep and 121mm long. The model uses hydrogen as fuel, the fuel injection pressure is 1.5MPa, and the equivalence ratio is about 0.1. In non-combustion flow ( Figure 4 Schlieren diagram), when the supersonic gas flow flows through the cavity 2 area, an expansion wave structure is generated at the step of the cavity 2. The shear layer (B) at the lower part of the cavity 2 is in contact with the bottom of the cavity 2. When the high-speed air flow further flows through the slope of the rear edge of the cavity 2, an oblique shock wave system (C) is generated, which is connected with the bottom of the engine. The wall boundary layer interacts, and the oblique shock wave is reflected by the wall. A separation ...
PUM
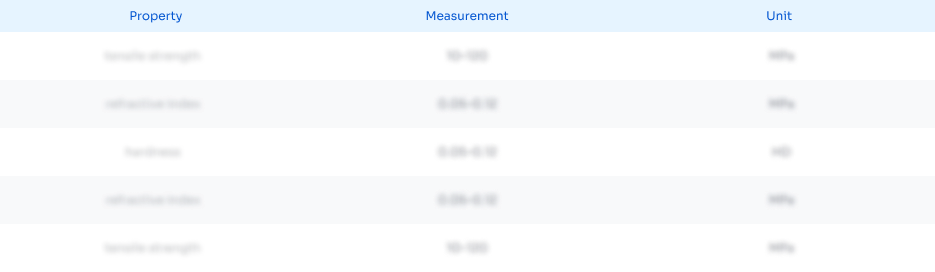
Abstract
Description
Claims
Application Information

- Generate Ideas
- Intellectual Property
- Life Sciences
- Materials
- Tech Scout
- Unparalleled Data Quality
- Higher Quality Content
- 60% Fewer Hallucinations
Browse by: Latest US Patents, China's latest patents, Technical Efficacy Thesaurus, Application Domain, Technology Topic, Popular Technical Reports.
© 2025 PatSnap. All rights reserved.Legal|Privacy policy|Modern Slavery Act Transparency Statement|Sitemap|About US| Contact US: help@patsnap.com