Machining method of supporting sleeve and supporting sleeve
A processing method and technology of support sleeve, which are applied in the direction of fluid pressure actuating device, etc., can solve the problems of affecting the working efficiency and service life of the breaker, affecting the matching clearance between the copper sleeve and the piston, increasing the processing cost of the support sleeve, etc., so as to reduce the processing cost. Cost, good guiding and supporting effect, and the effect of convenient processing
- Summary
- Abstract
- Description
- Claims
- Application Information
AI Technical Summary
Problems solved by technology
Method used
Image
Examples
Embodiment 1
[0064] Example 1, such as Figure 5-Figure 12 As shown, a processing method for a support sleeve includes the following steps:
[0065] 1) Process the support sleeve base 1 and the annular retaining ring 2, and process the ring platform 11 and the inclined surface 12 on the support sleeve base;
[0066] 2) Fix the annular retaining ring 2 on the ring platform 11, so that an annular cavity 3 is formed between the annular retaining ring 2 and the support sleeve base 1;
[0067] 3) Copper alloy or copper material is evenly distributed on the upper part of the annular cavity, and then the support sleeve matrix with copper alloy or copper material is placed in a sintering furnace for sintering. The sintering temperature is 1000-1150 degrees, and the sintering time is 2-5h, the copper sleeve blank 4 is formed in the annular cavity after the copper alloy or copper material is sintered;
[0068] 4) Machining to form a semi-finished support sleeve;
[0069] 5) nitriding treatment, p...
Embodiment 2
[0077] Example 2, such as Figure 13 As shown, the inner diameter of the ring seat processed in step 1) is smaller than the outer diameter of the annular retaining ring. In this case, the annular retaining ring can be fixed directly on the ring platform. The rest of the steps are the same as in Example 1 and will not be repeated here.
Embodiment 3
[0078] Example 3, such as Figure 14 As shown, step 1) also includes processing at least one ring groove 13 on the support base. The melting of copper alloy or copper material can enter the ring groove, further increasing the bonding strength between the copper sleeve and the base of the support sleeve. The rest of the steps are the same as in Example 1 and will not be repeated here.
[0079] At least one annular groove 17 is provided on the base of the support sleeve processed by the embodiment 3, and an annular protrusion matching the annular groove is provided on the copper sleeve. The tight combination between the copper sleeve and the supporting sleeve base further increases the bonding strength between the copper sleeve and the supporting sleeve base to prevent the loosening of the copper sleeve, thereby preventing the wear between the piston and the cylinder and prolonging the service life of the breaker.
PUM
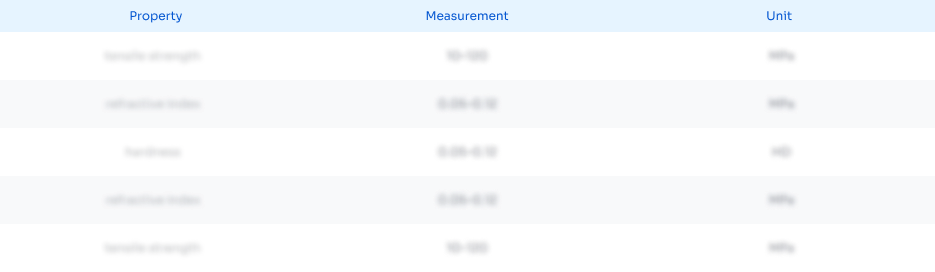
Abstract
Description
Claims
Application Information

- R&D Engineer
- R&D Manager
- IP Professional
- Industry Leading Data Capabilities
- Powerful AI technology
- Patent DNA Extraction
Browse by: Latest US Patents, China's latest patents, Technical Efficacy Thesaurus, Application Domain, Technology Topic, Popular Technical Reports.
© 2024 PatSnap. All rights reserved.Legal|Privacy policy|Modern Slavery Act Transparency Statement|Sitemap|About US| Contact US: help@patsnap.com