Robot automatic welding process for container ripple welding
An automatic welding and robotic technology, applied in welding equipment, welding accessories, manufacturing tools, etc., can solve problems such as research and effective progress, and achieve the effects of good welding quality, high welding precision, and convenient output
- Summary
- Abstract
- Description
- Claims
- Application Information
AI Technical Summary
Problems solved by technology
Method used
Image
Examples
Embodiment Construction
[0042] In this embodiment, a robot automatic welding process for corrugated welding of containers, the object to be processed is a wallboard to be welded (including regular structure plates and irregular structure plates, such as figure 1 The frame 1a and the corrugated plate 2a shown), the welding equipment used includes the central control system and the robot body, combined with Figure 4 and Figure 5 , the robot body 1 is driven and controlled by the central control system through the controller, the robot body 1 is provided with a welding torch 2 and a scanning identification unit 3, combined with Figure 6 , the scanning recognition unit 3 includes a double-point laser sensor formed by a laser sensor one 31 and a laser sensor two 32, the two-point laser sensor is connected to the central control system, and controls the wire feeder to supply solder and the movement of the welding torch according to the scanning signal of the two-point laser sensor track,
[0043] comb...
PUM
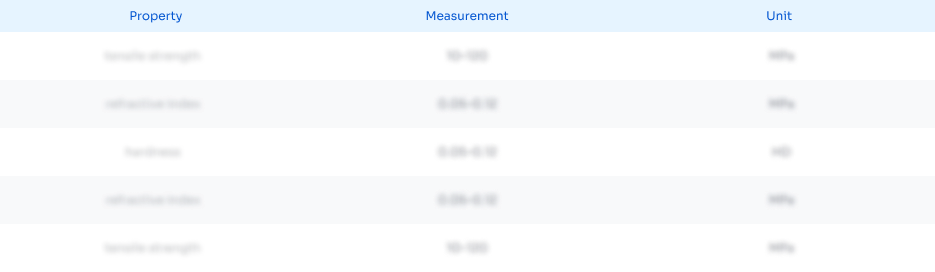
Abstract
Description
Claims
Application Information

- R&D
- Intellectual Property
- Life Sciences
- Materials
- Tech Scout
- Unparalleled Data Quality
- Higher Quality Content
- 60% Fewer Hallucinations
Browse by: Latest US Patents, China's latest patents, Technical Efficacy Thesaurus, Application Domain, Technology Topic, Popular Technical Reports.
© 2025 PatSnap. All rights reserved.Legal|Privacy policy|Modern Slavery Act Transparency Statement|Sitemap|About US| Contact US: help@patsnap.com