Installation method of high-pressure detachable cover plate type heat exchanger tube box
A technology of heat exchanger tube and installation method, applied in the direction of heat exchanger type, heat exchanger shell, indirect heat exchanger, etc., to achieve the effect of avoiding single-sided force and uniform force
- Summary
- Abstract
- Description
- Claims
- Application Information
AI Technical Summary
Problems solved by technology
Method used
Image
Examples
Embodiment 1
[0017] The middle part of the pipe box 1 is provided with an intermediate partition 4, the upper end of the pipe box 1 is provided with a flange 2, and the upper surface of the pipe box 1 is provided with a rectangular boss sealing surface 3, and the inner side of the rectangular boss sealing surface 3 is evenly distributed with ear-shaped boss sealing surfaces 3.1 , the rectangular boss sealing surface 3 is integrally formed with the ear-shaped boss sealing surface to form the boss sealing surface, the inner screw hole 5 is set in the middle of the ear-shaped boss sealing surface 3.1, the upper end of the pipe box 1 is provided with a cover plate 6, and the cover plate 6 is close to the surroundings The outer screw holes 11 are evenly distributed on the edge, the lower surface of the cover plate 6 is provided with a rectangular groove sealing surface 9, the inner side of the rectangular groove sealing surface 9 is provided with an ear-shaped groove sealing surface 10, and the m...
Embodiment 2
[0019] Sealing pads 7 are evenly distributed between the groove sealing surface and the boss sealing surface.
Embodiment 3
[0021] Place the gasket 7 in the sealing surface of the groove, install the outer bolt 8 on the outer screw hole 11 of the cover plate 6 and the screw hole on the flange 2, and install the outer bolt 8 on the inner screw hole 5 on the cover plate 6 and the inner screw hole on the pipe box 1 The screw hole 5 corresponds to the installation of the inner bolt 8.1. The cover plate 6 is connected with the pipe box 1 through the outer bolt 8 and the inner bolt 8.1. The gasket 7 is pressed tightly, and the outer bolt 8 and the inner bolt 8.1 are located between two adjacent gaskets 7, which can ensure that the gasket 7 is evenly stressed and deformed uniformly, and can avoid single-sided force and local deformation of the gasket 7 If the problem is too large, the purpose of effective sealing is achieved. Under high-pressure conditions, the outer bolt 8 and the inner bolt 8.1 are stressed at the same time to ensure that the gasket 7 is evenly stressed in the sealing surface and realize...
PUM
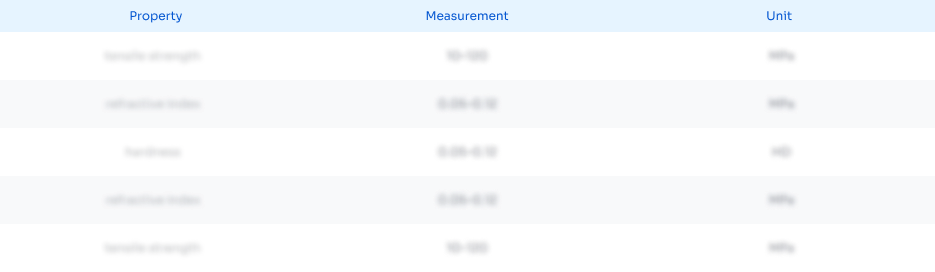
Abstract
Description
Claims
Application Information

- R&D Engineer
- R&D Manager
- IP Professional
- Industry Leading Data Capabilities
- Powerful AI technology
- Patent DNA Extraction
Browse by: Latest US Patents, China's latest patents, Technical Efficacy Thesaurus, Application Domain, Technology Topic, Popular Technical Reports.
© 2024 PatSnap. All rights reserved.Legal|Privacy policy|Modern Slavery Act Transparency Statement|Sitemap|About US| Contact US: help@patsnap.com