Large box plate type communication cabin structure
A technology of communication cabins and box panels, which is applied in the direction of artificial satellites, space navigation equipment, space navigation vehicles, etc., can solve the problems of low structural efficiency, small load-carrying capacity of pure cabin-type partial joints, long force transmission path, etc., and achieve improved Structural efficiency, guaranteed assembly manufacturability, direct effect of force transmission path
- Summary
- Abstract
- Description
- Claims
- Application Information
AI Technical Summary
Problems solved by technology
Method used
Image
Examples
Embodiment
[0046] The cabin structure of the present invention is made up of honeycomb sandwich structure board, is divided into dividing plate (north-south dividing plate 101, lower cabin east+Y shearing plate 102, lower cabin west-Y shearing plate 103, Lower cabin east-Y shearing plate 104, lower cabin west+Y shearing plate 105, east lower horizontal plate 106, west lower horizontal plate 107, middle cabin east partition 108, middle cabin west partition 109, upper horizontal plate 110, antenna Cabin north-south partition 201, antenna compartment east partition 202, antenna compartment west partition 203) and outer panels (south panel 111, north panel 112, opposite floor 204, east lower panel 301, west lower panel 401, east middle+Y Board 302, west middle-Y board 402, east middle-Y board 303, west middle+Y board 403, east upper board 304, west upper board 404, antenna cabin to floor 204), the cabin space is covered by 2 layers of horizontal boards ( East lower horizontal plate 106, west...
PUM
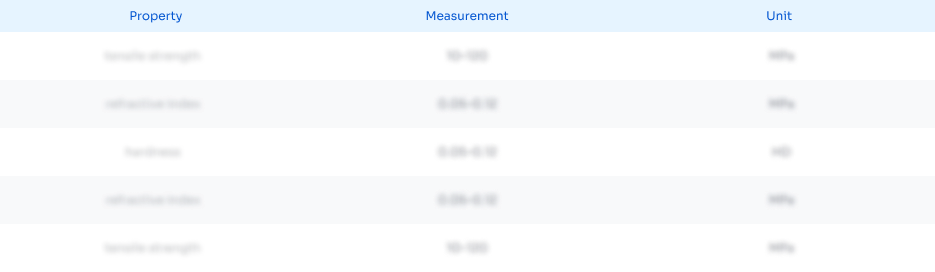
Abstract
Description
Claims
Application Information

- Generate Ideas
- Intellectual Property
- Life Sciences
- Materials
- Tech Scout
- Unparalleled Data Quality
- Higher Quality Content
- 60% Fewer Hallucinations
Browse by: Latest US Patents, China's latest patents, Technical Efficacy Thesaurus, Application Domain, Technology Topic, Popular Technical Reports.
© 2025 PatSnap. All rights reserved.Legal|Privacy policy|Modern Slavery Act Transparency Statement|Sitemap|About US| Contact US: help@patsnap.com