Continuous extrusion forming process for small-square-area brass special-shaped wire
A technology of extrusion molding and wire rod, which is applied in the field of continuous extrusion molding of small square brass special-shaped wire rods, can solve problems such as unstable quality, complicated process, labor and time-consuming, etc., and achieve improved product quality, simple process, and low energy consumption. small effect
- Summary
- Abstract
- Description
- Claims
- Application Information
AI Technical Summary
Problems solved by technology
Method used
Image
Examples
Embodiment 1
[0046] This embodiment provides a continuous extrusion molding process for a small square brass special-shaped wire rod, which is used to produce a small square brass special-shaped wire rod, which mainly includes the following steps:
[0047] 1) Preheating forming mold
[0048] Install the forming mold in a cavity, keep the forming mold flat in the cavity, put it into an electric heating box and heat it to 300°C, and then keep the constant temperature for 1h.
[0049] Among them, the specific heating process of the electric heating box is: first raise the temperature to between 100°C and 110°C, keep it for 10 minutes, then raise the temperature to 302°C, then lower the temperature to 300°C, and keep the constant temperature.
[0050] 2) Extrusion molding
[0051] Install the chamber after constant temperature treatment in the shoe seat of the extruder, check the pipeline of the extruder and turn on the extruder, take a number of heated brass rods with a length of 15cm, and a...
Embodiment 2
[0075] This embodiment provides a continuous extrusion molding process for a small square brass special-shaped wire rod, which is used to produce a small square brass special-shaped wire rod, which mainly includes the following steps:
[0076] 1) Preheating forming mold
[0077] Install the forming mold in a cavity, keep the forming mold flat in the cavity, put it into an electric heating box and heat it to 300°C, and then keep it for 1.2h.
[0078] Among them, the specific heating process of the electric heating box is: first raise the temperature to 105°C, keep it for 12 minutes, then raise the temperature to 304°C, then lower the temperature to 300°C, and keep the constant temperature.
[0079] 2) Extrusion molding
[0080] Install the chamber after constant temperature treatment in the shoe seat of the extruder, check the pipeline of the extruder and turn on the extruder, take a number of heated brass rods with a length of 20cm, and adjust the speed of the extruder to 6r / ...
Embodiment 3
[0104] This embodiment provides a continuous extrusion molding process for a small square brass special-shaped wire rod, which is used to produce a small square brass special-shaped wire rod, which mainly includes the following steps:
[0105] 1) Preheating forming mold
[0106] Install the forming mold in a cavity, keep the forming mold flat in the cavity, put it into an electric heating box and heat it to 300°C, and then keep the constant temperature for 1.5h.
[0107] Among them, the specific heating process of the electric heating box is: first raise the temperature to 110°C, keep it for 15 minutes, then raise the temperature to 305°C, then lower the temperature to 300°C, and keep the constant temperature.
[0108] 2) Extrusion molding
[0109] Install the chamber after constant temperature treatment in the shoe seat of the extruder, check the pipeline of the extruder and turn on the extruder, take a number of heated brass rods with a length of 20cm, and adjust the speed ...
PUM
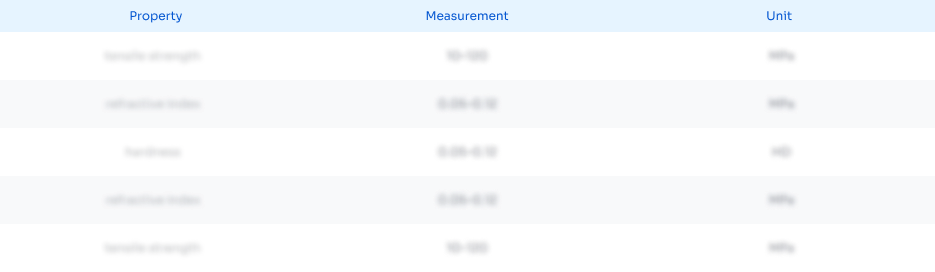
Abstract
Description
Claims
Application Information

- R&D
- Intellectual Property
- Life Sciences
- Materials
- Tech Scout
- Unparalleled Data Quality
- Higher Quality Content
- 60% Fewer Hallucinations
Browse by: Latest US Patents, China's latest patents, Technical Efficacy Thesaurus, Application Domain, Technology Topic, Popular Technical Reports.
© 2025 PatSnap. All rights reserved.Legal|Privacy policy|Modern Slavery Act Transparency Statement|Sitemap|About US| Contact US: help@patsnap.com