A cutting head follow-up control system and method
A cutting head and laser cutting head technology, which is applied in manufacturing tools, metal processing equipment, welding equipment, etc., can solve the problems of temperature, untimely feedback, and low accuracy of the follow-up control system, and achieve improved accuracy, good monitoring, The effect of facilitating later maintenance and management
- Summary
- Abstract
- Description
- Claims
- Application Information
AI Technical Summary
Problems solved by technology
Method used
Image
Examples
Embodiment Construction
[0028] Unless otherwise defined, all technical and scientific terms used herein have the same meaning as commonly understood by one of ordinary skill in the art of this application; terms used herein in the specification of the application are for the purpose of describing particular embodiments only , is not intended to limit the application; the terms "comprising" and "having" and any variations thereof in the description and claims of this application and the above description of the drawings are intended to cover non-exclusive inclusion. The terms "first", "second" and the like in the description and claims of the present application or the above drawings are used to distinguish different objects, rather than to describe a specific order.
[0029] Reference herein to an "embodiment" means that a particular feature, structure, or characteristic described in connection with the embodiment can be included in at least one embodiment of the present application. The appearances ...
PUM
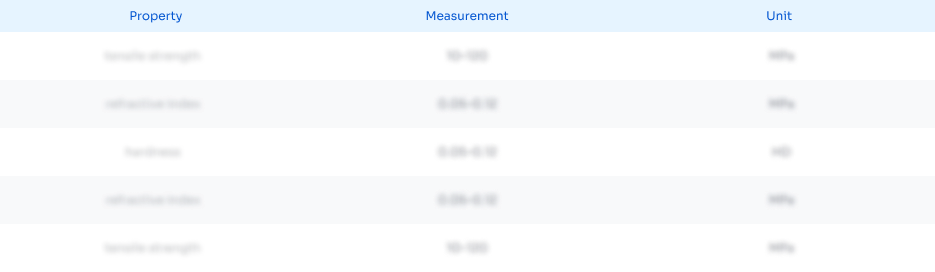
Abstract
Description
Claims
Application Information

- R&D Engineer
- R&D Manager
- IP Professional
- Industry Leading Data Capabilities
- Powerful AI technology
- Patent DNA Extraction
Browse by: Latest US Patents, China's latest patents, Technical Efficacy Thesaurus, Application Domain, Technology Topic, Popular Technical Reports.
© 2024 PatSnap. All rights reserved.Legal|Privacy policy|Modern Slavery Act Transparency Statement|Sitemap|About US| Contact US: help@patsnap.com