Control method of steel structure welding quality management and control system
A welding quality and control system technology, applied in welding equipment, welding equipment, welding accessories, etc., can solve problems such as irregular operation, uncontrollable quality, supervision, guarantee, guarantee, and violation of quality assurance, so as to achieve reliable storage environment, The effect of convenient and quick stock picking and standardized management
- Summary
- Abstract
- Description
- Claims
- Application Information
AI Technical Summary
Problems solved by technology
Method used
Image
Examples
Embodiment 1
[0049] This embodiment discloses a control method for a steel structure welding quality control system. The quality control system mainly includes five parts, which are the background terminal system 0 used as the overall process control and the interactive communication with the background terminal system 0. The intelligent storage sending machine 1, intelligent welding machine 2, intelligent temporary storage machine 3 and intelligent recycling machine 4; the intelligent storage sending machine 1, intelligent welding machine 2, intelligent temporary storage machine 3 and intelligent recycling machine 4 are all respectively Equipped with an industrial control all-in-one machine, and can realize real-time interaction with the background terminal system 0 through the industrial control all-in-one machine to realize the transmission of signals and instructions. The quality control system of the present embodiment also includes a hand-held terminal system, and the hand-held termin...
PUM
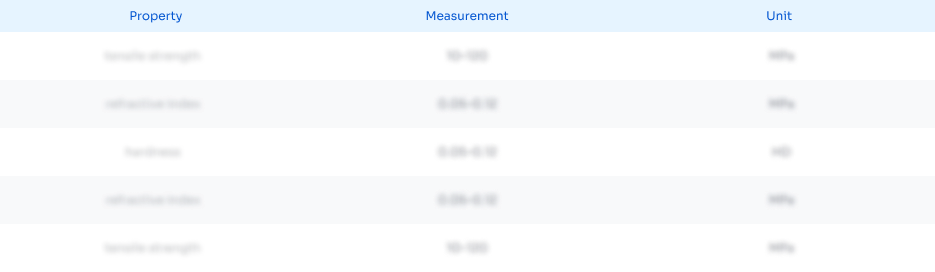
Abstract
Description
Claims
Application Information

- R&D
- Intellectual Property
- Life Sciences
- Materials
- Tech Scout
- Unparalleled Data Quality
- Higher Quality Content
- 60% Fewer Hallucinations
Browse by: Latest US Patents, China's latest patents, Technical Efficacy Thesaurus, Application Domain, Technology Topic, Popular Technical Reports.
© 2025 PatSnap. All rights reserved.Legal|Privacy policy|Modern Slavery Act Transparency Statement|Sitemap|About US| Contact US: help@patsnap.com