Transportation robot
A robot and inner bushing technology, applied in the field of transportation robots, can solve the problems of AGV's low speed, inflexible steering, and poor ability to overcome obstacles, etc., and achieve the effect of sufficient power performance, avoiding the phenomenon of suspension, and increasing the speed
- Summary
- Abstract
- Description
- Claims
- Application Information
AI Technical Summary
Problems solved by technology
Method used
Image
Examples
Embodiment Construction
[0036]The technical solutions in the present invention are clearly and completely described below in combination with the accompanying drawings in the embodiments of the present invention. Obviously, the described embodiments are only some of the embodiments of the present invention, not all of them. Based on the embodiments of the present invention, all other embodiments obtained by persons of ordinary skill in the art without creative efforts fall within the protection scope of the present invention.
[0037] Such as figure 1 with 2 As shown, a transportation robot provided in this embodiment includes a car body 200 , driving wheels, an electronic control module 500 , a power module 400 , a steering assembly and a suspension mechanism 260 mounted on the car body 200 . The vehicle body 200 includes a vehicle frame 210, the electronic control module 500 and the power supply module 400 are arranged at the bottom of the vehicle frame 210, the reducer 230 of the steering assembl...
PUM
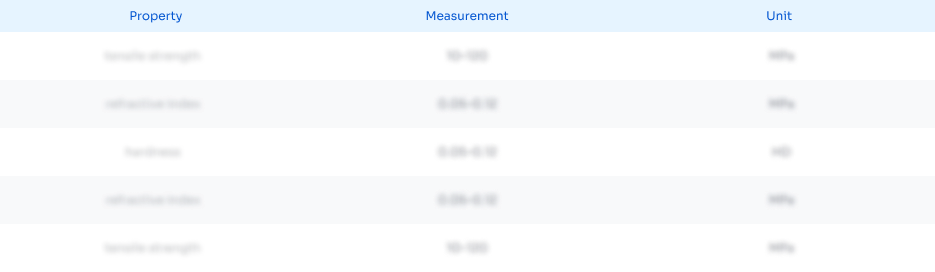
Abstract
Description
Claims
Application Information

- R&D Engineer
- R&D Manager
- IP Professional
- Industry Leading Data Capabilities
- Powerful AI technology
- Patent DNA Extraction
Browse by: Latest US Patents, China's latest patents, Technical Efficacy Thesaurus, Application Domain, Technology Topic, Popular Technical Reports.
© 2024 PatSnap. All rights reserved.Legal|Privacy policy|Modern Slavery Act Transparency Statement|Sitemap|About US| Contact US: help@patsnap.com