Machining method used for aviation composite parts
A processing method and parts technology, which is applied in the processing field of aerospace composite parts, can solve the problems of poor surface quality, wire stripping, and difficult processing of parts, so as to improve surface quality and trimming contour accuracy, improve positioning accuracy and processing Efficiency, product quality stable and reliable effect
- Summary
- Abstract
- Description
- Claims
- Application Information
AI Technical Summary
Problems solved by technology
Method used
Examples
Embodiment Construction
[0015] In order to make the purpose, technical solutions and advantages of the embodiments of the present invention more clear, the technical solutions in the embodiments of the present invention are clearly and completely described. Apparently, the described embodiments are some, but not all, embodiments of the present invention.
[0016] Accordingly, the following detailed description of the embodiments of the invention provided is not intended to limit the scope of the claimed invention, but represents only selected embodiments of the invention. Based on the embodiments of the present invention, all other embodiments obtained by persons of ordinary skill in the art without creative efforts fall within the protection scope of the present invention.
[0017] In the description of the present invention, it should be understood that the orientation or positional relationship indicated by the terms "upper", "lower", "inner", "outer", "left", "right" etc. The orientation or posi...
PUM
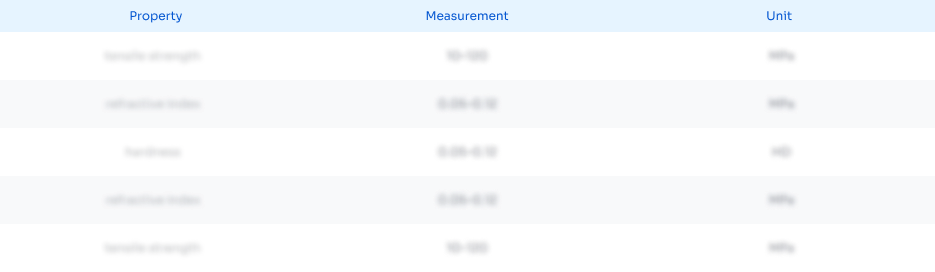
Abstract
Description
Claims
Application Information

- R&D
- Intellectual Property
- Life Sciences
- Materials
- Tech Scout
- Unparalleled Data Quality
- Higher Quality Content
- 60% Fewer Hallucinations
Browse by: Latest US Patents, China's latest patents, Technical Efficacy Thesaurus, Application Domain, Technology Topic, Popular Technical Reports.
© 2025 PatSnap. All rights reserved.Legal|Privacy policy|Modern Slavery Act Transparency Statement|Sitemap|About US| Contact US: help@patsnap.com