Injection molding method and device for preparing large-size high-temperature-resistant and high-pressure-resistant expansion coated capsule from ultrahigh-viscosity silicone rubber
A technology of injection molding and silicone rubber, which is applied in the fields of two-component injection molding equipment, molds, composite materials, and rubber injection molding. It can solve problems such as poor storage and uneven mixing of two-component high-viscosity rubber, and reduce production costs. The method is simple and easy to understand, and the effect of experimental controllability is strong
- Summary
- Abstract
- Description
- Claims
- Application Information
AI Technical Summary
Problems solved by technology
Method used
Image
Examples
Embodiment Construction
[0023] The technical solutions in the embodiments of the present invention will be described in detail below with reference to the drawings in the embodiments of the present invention. Wherein, the described embodiments are only some embodiments of the present invention, not all embodiments.
[0024] figure 1 Shown is a schematic diagram of the injection molding method and the overall structure of the device for preparing large-sized high-temperature-resistant and high-pressure-resistant expansion-coated capsules using ultra-high-viscosity silicone rubber; including a two-component resin tank 1, an extrusion device 2, a vacuum device 3, and a mixing device 4. Mold 5. Material A and material B are separately stored in a two-component resin tank 1, the upper end of the storage box is connected to the vacuum device 3, the lower end of the storage box is connected to the extrusion device 2, and the extrusion device 2 is connected to multiple mixing devices 4, mixing Device 21 is...
PUM
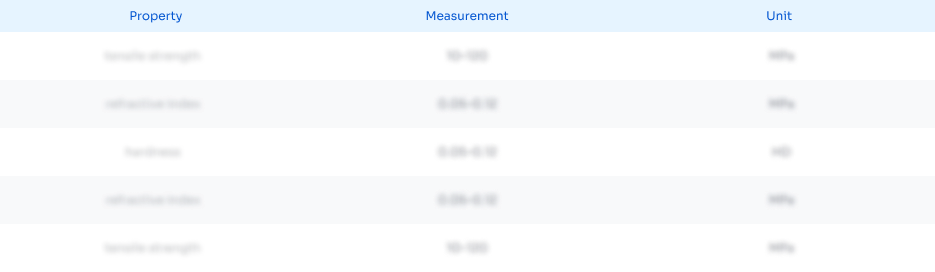
Abstract
Description
Claims
Application Information

- Generate Ideas
- Intellectual Property
- Life Sciences
- Materials
- Tech Scout
- Unparalleled Data Quality
- Higher Quality Content
- 60% Fewer Hallucinations
Browse by: Latest US Patents, China's latest patents, Technical Efficacy Thesaurus, Application Domain, Technology Topic, Popular Technical Reports.
© 2025 PatSnap. All rights reserved.Legal|Privacy policy|Modern Slavery Act Transparency Statement|Sitemap|About US| Contact US: help@patsnap.com