Spacecraft surface heat flow non-contact measurement method based on vacuum thermal test
A technology of non-contact measurement and vacuum thermal test, applied in the field of heat flow measurement and non-contact measurement of heat flow on the surface of spacecraft, it can solve the problems of measurement error, uneven distribution of heat flow density, and inability to guarantee the accuracy of heat flow simulation, and achieve accurate heat flow values. , the effect of improving the effectiveness
- Summary
- Abstract
- Description
- Claims
- Application Information
AI Technical Summary
Problems solved by technology
Method used
Image
Examples
Embodiment Construction
[0035] The present invention will be further described in detail below in conjunction with the accompanying drawings and embodiments. It should be understood that the specific embodiments described here are only used to explain related inventions, rather than to limit the invention. It should also be noted that, for ease of description, only parts related to the invention are shown in the drawings.
[0036] It should be noted that, in the case of no conflict, the embodiments of the present invention and the features in the embodiments can be combined with each other. The present invention will be described in detail below with reference to the accompanying drawings and examples.
[0037] The present invention proposes a non-contact measurement method for heat flow on the surface of a spacecraft based on a vacuum thermal test for the measurement of heat flow on the surface of a spacecraft that cannot be equipped with a heat flow meter in a vacuum thermal test, such as figure...
PUM
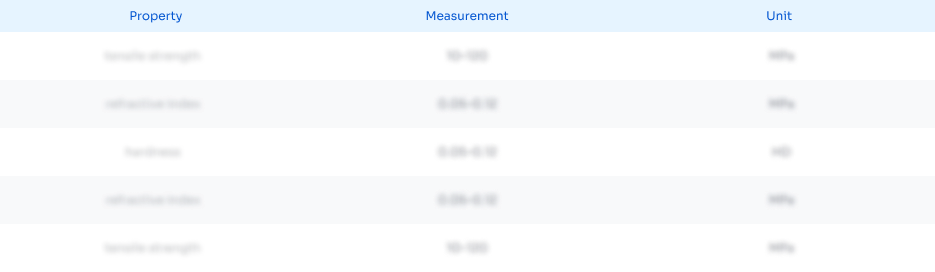
Abstract
Description
Claims
Application Information

- R&D
- Intellectual Property
- Life Sciences
- Materials
- Tech Scout
- Unparalleled Data Quality
- Higher Quality Content
- 60% Fewer Hallucinations
Browse by: Latest US Patents, China's latest patents, Technical Efficacy Thesaurus, Application Domain, Technology Topic, Popular Technical Reports.
© 2025 PatSnap. All rights reserved.Legal|Privacy policy|Modern Slavery Act Transparency Statement|Sitemap|About US| Contact US: help@patsnap.com