Realization method of aeroelastic optimal design of turbomachinery considering random detuning
A technology of aeroelasticity and impeller machinery, applied in computer-aided design, design optimization/simulation, multi-objective optimization, etc., can solve problems such as blade fatigue failure, accidents, blade cracks, etc., to reduce sensitivity, improve life, and reduce forced Effect of Vibration Amplitude
- Summary
- Abstract
- Description
- Claims
- Application Information
AI Technical Summary
Problems solved by technology
Method used
Image
Examples
Embodiment Construction
[0047] Such as figure 1 As shown, this embodiment relates to an optimal design method of turbomachinery aeroelasticity including random detuning, including the following steps:
[0048] Step 1: Select an axial fan blade, and use the function (blade parameter extraction unit) written by Matlab to parameterize the original blade.
[0049] Step 2: Experimental design: According to the number of blade design variables and the upper and lower limits of each variable, use Latin hypercube sampling to generate an appropriate number of experiments.
[0050] Step 3: Use the custom Matlab function to drive the Turbogrid module in the computational fluid dynamics software CFX to divide the single-channel grid of the flow field, such as figure 2 shown. The surface of the blade is an O-shaped grid, and the grid scale meets the requirement that Y+ is less than 5. Import the single-channel flow field grid into CFX-Pre, and use Turbo Rotation to copy (N-1) grids with the rotation axis to o...
PUM
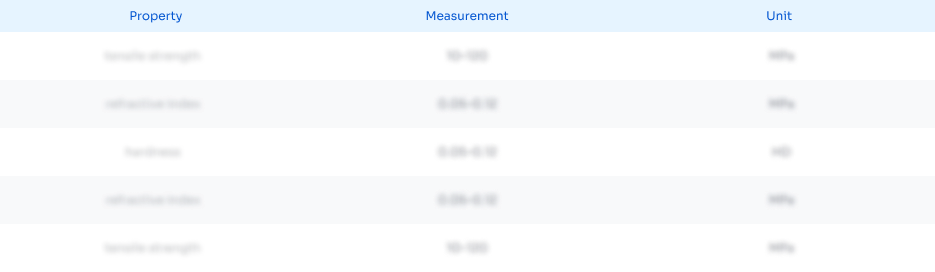
Abstract
Description
Claims
Application Information

- R&D
- Intellectual Property
- Life Sciences
- Materials
- Tech Scout
- Unparalleled Data Quality
- Higher Quality Content
- 60% Fewer Hallucinations
Browse by: Latest US Patents, China's latest patents, Technical Efficacy Thesaurus, Application Domain, Technology Topic, Popular Technical Reports.
© 2025 PatSnap. All rights reserved.Legal|Privacy policy|Modern Slavery Act Transparency Statement|Sitemap|About US| Contact US: help@patsnap.com