Rapid modeling method for composite material tool compensation profile simulation verification
A composite material, simulation verification technology, applied in the field of rapid modeling of composite material tooling compensation profile simulation verification, can solve the problems of poor creation accuracy, troublesome operation, no correspondence of geometric theoretical profiles, etc., to improve verification efficiency and Accuracy, to achieve the effect of compensation effect comparison
- Summary
- Abstract
- Description
- Claims
- Application Information
AI Technical Summary
Problems solved by technology
Method used
Image
Examples
Embodiment 1
[0032] This embodiment discloses a rapid modeling method for the simulation verification of composite material tooling compensation surface, refer to the attached figure 1 , mainly including the following steps:
[0033] Step S1: Simulation Analysis of Theoretical Model of Composite Material Parts
[0034] In the finite element software, the theoretical geometric model is modeled and simulated according to the simulation process, and the INP file of the theoretical geometric model is obtained;
[0035] Step S2: Post-processing of theoretical model simulation analysis results
[0036] In the post-processing of the finite element software, the relevant data information before and after the solidification and deformation of the theoretical geometric model is exported to form a data file;
[0037] Step S3: Processing Data Files
[0038] Identify the node, element, entity and other data in the node RPT file, element RPT file and simulation model INP file, and form a one-to-one c...
Embodiment 2
[0047] This embodiment discloses a rapid modeling method for the simulation verification of composite material tooling compensation surface. This embodiment is optimized on the basis of Embodiment 1. In the step S1, the mesh model of the part needs to be maintained The same stretch thickness, same stretch layer number and opposite stretch direction as tooling mesh model.
[0048] Further, in order to better realize this application, the data file in the step S2 refers to exporting the data information (node and element) of all mesh nodes of the deformed part model and the film surface of the part to form a simulation result RPT file (Including node RPT file and element RPT file), which contains information such as the node coordinate value of the model, the relationship between nodes and elements, and the amount of deformation. At the same time, the INP for the simulation analysis of the theoretical model of the composite material part will be automatically generated in the c...
Embodiment 3
[0056] This embodiment discloses a rapid modeling method for the simulation verification of composite material tooling compensation surface, refer to the attached figure 1 , mainly including the following steps:
[0057] Step S1: Simulation Analysis of Theoretical Model of Composite Material Parts
[0058] In ABAQUS, the theoretical geometric model is modeled and simulated according to the simulation process, and the simulation model INP file of the theoretical geometric model is obtained.
[0059] In this embodiment, the simulation analysis software ABAQUS is used to divide the finite element mesh of the composite material parts, and the mesh model of the composite material parts and forming tooling is realized through the mesh part and offset functions, and the material parameters, process parameters and boundary constraints are set , to achieve simulation analysis of composite parts. After calculation and analysis, the simulation model INP file including all composite mat...
PUM
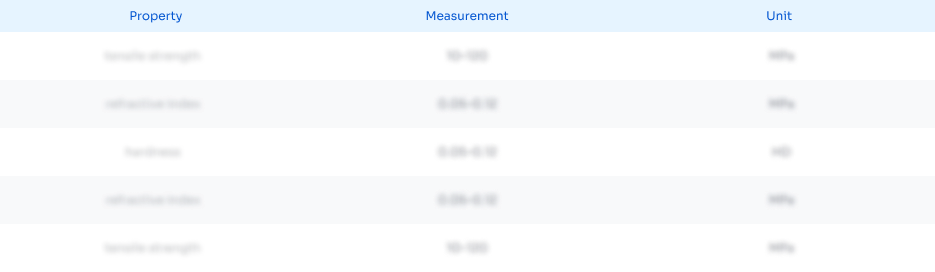
Abstract
Description
Claims
Application Information

- R&D
- Intellectual Property
- Life Sciences
- Materials
- Tech Scout
- Unparalleled Data Quality
- Higher Quality Content
- 60% Fewer Hallucinations
Browse by: Latest US Patents, China's latest patents, Technical Efficacy Thesaurus, Application Domain, Technology Topic, Popular Technical Reports.
© 2025 PatSnap. All rights reserved.Legal|Privacy policy|Modern Slavery Act Transparency Statement|Sitemap|About US| Contact US: help@patsnap.com