Production technology of 6-series alloy bar for anodic oxidation
A production process, anodic oxidation technology, applied in the field of aluminum alloys, can solve problems such as limited degassing and slag removal, black lines, and poor surface quality of 6-series alloy rods, so as to strengthen production process control, reduce energy consumption, and enhance The effect of market competitiveness
- Summary
- Abstract
- Description
- Claims
- Application Information
AI Technical Summary
Problems solved by technology
Method used
Image
Examples
Embodiment 1
[0088]The specific steps are as follows:
[0089](1) Select electrolytic cell aluminum liquid with aluminum purity of 99.85% as raw materials. According to the mass percentage of each element in the 6 series alloy rod, the chemical composition content of the aluminum alloy is equipped. The content of each other impurity element is required to be less than 0.02%, and the total impurity content is less than 0.15%. The composition of Mg and Si in the aluminum liquid The ratio is between 1.1-1.7. The aluminum liquid in the electrolytic cell is liquid material.
[0090]The prepared aluminum alloy raw materials are added into a smelting furnace and uniformly stirred and mixed and then smelted into liquid aluminum alloy. The smelting temperature is controlled at 725°C. During the smelting process in the furnace, the stirring is strengthened, and the electromagnetic stirring time is extended to 40min to obtain the alloy aluminum liquid.
[0091](2) Refining: adding a refining agent to the alloy alum...
Embodiment 2
[0107]The specific steps are as follows:
[0108](1) Select electrolytic cell aluminum liquid with aluminum purity of 99.85% as raw materials. According to the mass percentage of each element in the 6 series alloy rod, the chemical composition content of the aluminum alloy is equipped, and the content of each other impurity element is required to be less than 0.02%, and the total impurity content is less than 0.15%. The aluminum liquid in the electrolytic cell is liquid material.
[0109]The prepared aluminum alloy raw materials are added into a smelting furnace and uniformly stirred and mixed and then smelted into liquid aluminum alloy. The smelting temperature is controlled at 719℃. During the smelting process in the furnace, the stirring is strengthened, and the electromagnetic stirring time is extended to 40min to obtain the alloy aluminum liquid.
[0110](2) Refining: adding a refining agent to the alloy aluminum liquid for refining. Refining agent consists of NaCl, NaNO3, Na2SO4, KCl, ...
Embodiment 3
[0123]The specific steps are as follows:
[0124](1) Select electrolytic cell aluminum liquid with aluminum purity of 99.85% as raw materials. According to the mass percentage of each element in the 6 series alloy rod, the chemical composition content of the aluminum alloy is equipped, and the content of each other impurity element is required to be less than 0.02%, and the total impurity content is less than 0.15%. The aluminum liquid in the electrolytic cell is liquid material.
[0125]The prepared aluminum alloy raw materials are added into a smelting furnace and uniformly stirred and mixed and then smelted into liquid aluminum alloy. The smelting temperature is controlled at 750℃. During the smelting process in the furnace, the stirring is strengthened, and the electromagnetic stirring time is extended to 40min to obtain the alloy aluminum liquid.
[0126](2) Refining: adding a refining agent to the alloy aluminum liquid for refining. Refining agent consists of NaCl, NaNO3, Na2SO4, KCl, ...
PUM
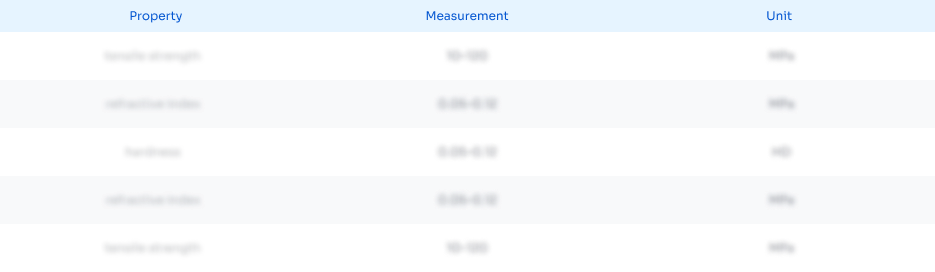
Abstract
Description
Claims
Application Information

- R&D
- Intellectual Property
- Life Sciences
- Materials
- Tech Scout
- Unparalleled Data Quality
- Higher Quality Content
- 60% Fewer Hallucinations
Browse by: Latest US Patents, China's latest patents, Technical Efficacy Thesaurus, Application Domain, Technology Topic, Popular Technical Reports.
© 2025 PatSnap. All rights reserved.Legal|Privacy policy|Modern Slavery Act Transparency Statement|Sitemap|About US| Contact US: help@patsnap.com