Method for preparing battery-grade lithium carbonate from lepidolite
A lithium carbonate, battery-grade technology, applied in the direction of lithium carbonate;/acid carbonate, etc., can solve the problems of difficult control of Ca and Mg impurity content, fluctuation of product quality, and inability of products to reach batteries, etc. Prospects for industrialization, low cost, and the effect of less chemical raw materials
- Summary
- Abstract
- Description
- Claims
- Application Information
AI Technical Summary
Problems solved by technology
Method used
Image
Examples
Embodiment 1
[0025] A method utilizing lepidolite to prepare battery-grade lithium carbonate, comprising the following steps:
[0026] (1) Fluoride removal: Lepidolite is roasted and leached to obtain the leachate, add a defluoride agent, stir evenly, after 50°C heat preservation and sufficient reaction, adjust the pH to 6.5, settle for 3 hours, and filter to obtain a lithium solution with reduced fluorine content, filter residue For roasting auxiliary materials;
[0027] (2) Preparation of refined lithium solution: the lithium solution with reduced fluorine content is purified, concentrated and evaporated to obtain a concentrated lithium solution, frozen to remove potassium and sodium at 10°C, and then treated with a chelating ion exchange resin to obtain a refined lithium solution;
[0028] (3) preparation of refined sodium carbonate solution: after the sodium carbonate solid is dissolved in water, control the carbonate concentration to be 155g / L, after press filtration, remove calcium a...
Embodiment 2
[0039] A method utilizing lepidolite to prepare battery-grade lithium carbonate, comprising the following steps:
[0040] (1) Fluoride removal: After lepidolite is roasted and leached, add a defluoride agent and stir evenly. After fully reacting at 60°C, adjust the pH to 5.5. After settling for 2 hours, filter to obtain a lithium solution with reduced fluorine content. For roasting auxiliary materials;
[0041] (2) Preparation of refined lithium solution: the lithium solution with reduced fluorine content is purified, concentrated and evaporated to obtain a concentrated lithium solution, frozen to remove potassium and sodium at 5°C, and then treated with a chelating ion exchange resin to obtain a refined lithium solution;
[0042] (3) preparation of refined sodium carbonate solution: after the sodium carbonate solid is dissolved in water, control the carbonate concentration to be 130g / L, after pressure filtration, remove calcium and magnesium through chelating ion exchange res...
Embodiment 3
[0053] A method utilizing lepidolite to prepare battery-grade lithium carbonate, comprising the following steps:
[0054] (1) Fluoride removal: after lepidolite is roasted and leached, add a defluoride agent and stir evenly. After fully reacting at 40°C, adjust the pH to 7.5. After settling for 4 hours, filter to obtain a lithium solution with reduced fluorine content. For roasting auxiliary materials;
[0055] (2) Preparation of refined lithium solution: the lithium solution with reduced fluorine content is purified, concentrated and evaporated to obtain a concentrated lithium solution, frozen to remove potassium and sodium at 0°C, and then treated with a chelating ion exchange resin to obtain a refined lithium solution;
[0056] (3) preparation of refined sodium carbonate solution: after the sodium carbonate solid is dissolved in water, control the carbonate concentration to be 180g / L, after press filtration, remove calcium and magnesium through chelating ion exchange resin ...
PUM
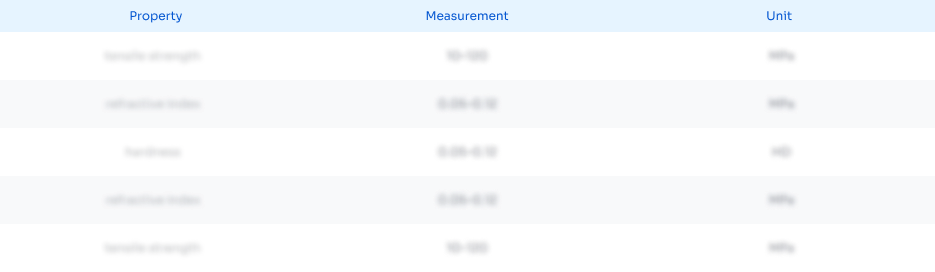
Abstract
Description
Claims
Application Information

- R&D Engineer
- R&D Manager
- IP Professional
- Industry Leading Data Capabilities
- Powerful AI technology
- Patent DNA Extraction
Browse by: Latest US Patents, China's latest patents, Technical Efficacy Thesaurus, Application Domain, Technology Topic, Popular Technical Reports.
© 2024 PatSnap. All rights reserved.Legal|Privacy policy|Modern Slavery Act Transparency Statement|Sitemap|About US| Contact US: help@patsnap.com