A bending system for automatic feeding and positioning of plates
An automatic material feeding and sheet metal technology, applied in the field of sheet metal processing, can solve problems such as error prone and troublesome positioning, achieve accurate and fast positioning, improve bending efficiency, and ensure processing accuracy
- Summary
- Abstract
- Description
- Claims
- Application Information
AI Technical Summary
Problems solved by technology
Method used
Image
Examples
Embodiment 1
[0041] As shown in the figure, a bending system for automatic feeding and positioning of plates is used for bending and processing of plates. It mainly includes four parts: a conveying device 1, a workpiece placing device 2, a feeding device 3 and a bending machine 4.
[0042] Among them, the feeding device 3 has at least one pair, and each pair of feeding devices 3 is symmetrically arranged on both sides of the bending machine 4 . Usually, at least two pairs of the feeding device 3 are generally arranged, and two pairs on the same side of the bending machine 4 are arranged. The feeding devices 3 are respectively arranged at the front and rear ends of the bending machine 4. By adjusting the pushing positions of the feeding devices 3 at the front and rear ends to the workpiece, the inclination of the workpiece entering the bending machine 4 can be adjusted to meet different processing requirements. The workpiece placing device 2 is arranged on one side of the bending machine 4, ...
Embodiment 2
[0056] The structure of the bending system for automatic feeding and positioning of plates in this embodiment is basically the same as that of Embodiment 1, and only the sensing mechanism of the blocking post 33 is improved. like image 3 and Figure 4 As shown, in this embodiment, the blocking post 33 realizes the positioning of the workpiece through the mechanical induction mechanism 35 .
[0057] The mechanical sensing mechanism 35 includes a rotating shaft 351 , a guide rod 352 , a connecting arm 353 , a sensing arm 354 and a sensor. The rotating shaft 351 is arranged vertically, and its upper and lower ends are hingedly connected to the upper and lower end surfaces of the box body 32 through rotating bearings. There are two guide rods 352 and two connecting arms 353 . The two connecting arms 353 are respectively sleeved on the upper part and the lower part of the rotating shaft 351 ; One end of the guide rod 352 is fixedly connected with the blocking post 33 , and the ...
Embodiment 3
[0061] A sheet metal automatic feeding positioning and bending method adopts the bending system for sheet automatic feeding positioning according to Embodiment 1 or Embodiment 2, and the process is as follows: the material transporting device 1 transports the workpiece to be processed from the workpiece placing device 2 to the workpiece placing device 2. After being located on the feeding device 3 on one side of the bending machine 4, the box drive mechanism in the feeding device 3 works, and the driving block 33 pushes the workpiece to move to the other side of the bending machine 4. After the stopper 33 on the device 3 touches the workpiece, the electronic control device simultaneously receives the signal from the feeding devices 3 on both sides of the bending machine 4 that the workpiece reaches the processing position, and controls the box drive mechanism to stop working, and the workpiece stays in the processing position. Location.
[0062] When the bending system of Embo...
PUM
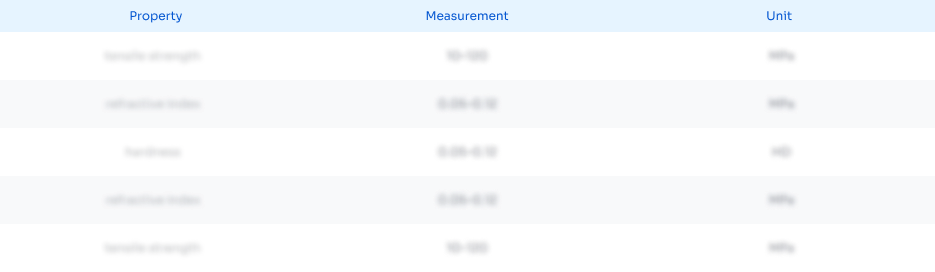
Abstract
Description
Claims
Application Information

- Generate Ideas
- Intellectual Property
- Life Sciences
- Materials
- Tech Scout
- Unparalleled Data Quality
- Higher Quality Content
- 60% Fewer Hallucinations
Browse by: Latest US Patents, China's latest patents, Technical Efficacy Thesaurus, Application Domain, Technology Topic, Popular Technical Reports.
© 2025 PatSnap. All rights reserved.Legal|Privacy policy|Modern Slavery Act Transparency Statement|Sitemap|About US| Contact US: help@patsnap.com