A kind of eps foam molding equipment
A foam molding and equipment technology, applied in the field of EPS foam preparation, can solve the problems of uneven specific gravity, uneven particle size of pre-expanded beads, uneven product density, etc., to achieve uniform specific gravity, small product density gradient, and particle size The effect of uniform size and specific gravity
- Summary
- Abstract
- Description
- Claims
- Application Information
AI Technical Summary
Problems solved by technology
Method used
Image
Examples
Embodiment
[0017] like Figure 1 to Figure 3 As shown, an EPS foam molding equipment includes a foaming box 1, a driving device 1 for feeding and blowing air to the foaming box 1, and a driving device 2 for discharging and blowing air to the foaming box 1 3 , the foaming box 1 is provided with a partition 11 and is divided into a foaming chamber 12 and a sorting chamber 13 by the partition 11, the top of the foaming chamber 12 is provided with a feed hopper 14 and its outside Air inlet pipe one 15 is provided, the bottom of the foaming chamber 12 is provided with a steam generator 16 and steam is injected into the foaming chamber 12 through the steam generator 16, between the top of the foaming chamber 12 and the dividing plate 11 Form inlet 17, the top of described sorting chamber 13 is equipped with collecting cover 18, and described collecting cover 18 upper end is communicated with negative pressure fan, and the bottom of described sorting chamber 13 is provided with discharge port 1...
PUM
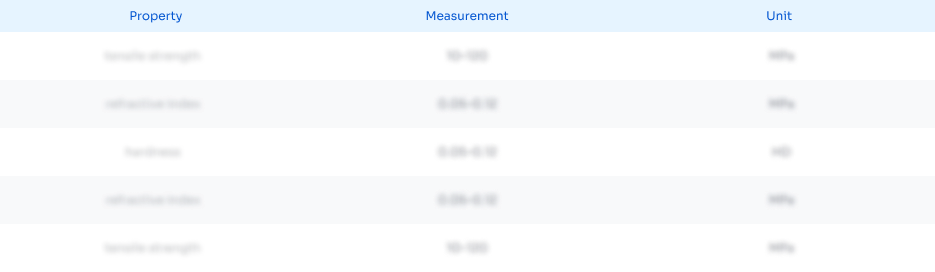
Abstract
Description
Claims
Application Information

- R&D
- Intellectual Property
- Life Sciences
- Materials
- Tech Scout
- Unparalleled Data Quality
- Higher Quality Content
- 60% Fewer Hallucinations
Browse by: Latest US Patents, China's latest patents, Technical Efficacy Thesaurus, Application Domain, Technology Topic, Popular Technical Reports.
© 2025 PatSnap. All rights reserved.Legal|Privacy policy|Modern Slavery Act Transparency Statement|Sitemap|About US| Contact US: help@patsnap.com