Shell series surface processing technology
A surface processing and shell technology, which is applied in the field of shell series surface processing technology, can solve the problems of easy to hide dirt during product use, many gaps between the bumps on the polished surface, and insufficient hand feeling, and achieve excellent antifouling performance, uniform gloss, Soft touch effect on the surface
- Summary
- Abstract
- Description
- Claims
- Application Information
AI Technical Summary
Problems solved by technology
Method used
Image
Examples
Embodiment
[0020] A shell series surface processing technology, comprising the following steps:
[0021] Step 1. Send the finished bricks to the box-type waste heat drying kiln installed in front of the firing kiln, extract the waste heat from the tail of the firing kiln to heat the drying kiln, and then use the automatic temperature measuring gun to test that the temperature in the drying kiln is 65 -75°C, keep the temperature and continue to dry for 20-30 minutes to complete the drying of the adobe. Finally, after testing, if the moisture content in the adobe is less than 0.7% of the total mass of the adobe, proceed to the next step of processing. If the content is greater than 0.7% of the total mass of the adobe, it will be returned to be dried and dewatered again;
[0022] Step 2. The dry and dewatered bricks in step 1 are replenished with water through the water spray cabinet, so that the surface of the bricks is moistened, which is conducive to the combination of the glaze and the ...
experiment example
[0032] The weather resistance of the surface of the slate is tested as shown in the following table:
[0033]
[0034] According to the above experiments, not only the glossiness of the surface of the rock slab of the present invention meets the requirements, but also its antifouling effect and hardness also meet the requirements.
[0035] The technical effect of the present invention is mainly reflected in the following aspects: the brick adobe laid by the press is dried for the first time to remove the free water inside, the moisture content in the adobe is controlled to be less than 0.7% of the total mass of the adobe, and the adobe is dried after it leaves the kiln. Spray water mist on the surface, then spray the bottom glaze on the surface of the green body, and then spray the pattern with an inkjet machine, spray the protective glaze and dry shells in sequence after drying in the drying kiln, and then go into the kiln for firing after the second drying in the drying ki...
PUM
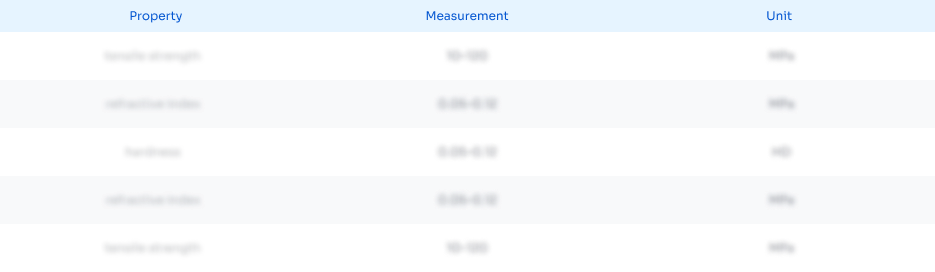
Abstract
Description
Claims
Application Information

- R&D Engineer
- R&D Manager
- IP Professional
- Industry Leading Data Capabilities
- Powerful AI technology
- Patent DNA Extraction
Browse by: Latest US Patents, China's latest patents, Technical Efficacy Thesaurus, Application Domain, Technology Topic, Popular Technical Reports.
© 2024 PatSnap. All rights reserved.Legal|Privacy policy|Modern Slavery Act Transparency Statement|Sitemap|About US| Contact US: help@patsnap.com