Method for improving wind power grid-connected primary frequency modulation performance by utilizing adaptive virtual parameters
A virtual parameter, self-adaptive technology, applied in the direction of wind power generation, electrical components, circuit devices, etc., can solve the problems of increasing response time, power oscillation suppression, affecting power oscillation suppression performance, etc., to achieve the problem of suppressing power oscillation, the value reasonable effect
- Summary
- Abstract
- Description
- Claims
- Application Information
AI Technical Summary
Problems solved by technology
Method used
Image
Examples
Embodiment Construction
[0045] The technical solution of the present invention will be described in further detail below with reference to the accompanying drawings.
[0046]Such as figure 1 As shown, the wind power generation system controls the inverter by imitating the drooping characteristics of the synchronous generator in the conventional generating set. In the frequency response process of the wind power generation system, due to the existence of the dead zone of the inverter device, it is necessary to set the frequency response action threshold f d , usually f d =(50±0.1)Hz, when the droop control output frequency is 49.9Hz≤f≤50.1Hz, the droop control system will not act. According to the output characteristics of the inverter, the adjustment range of the output active power of the wind power generation system during a frequency regulation is: ±10%P 0 , where: P 0 is the initial value of the output power of the primary frequency modulation of the fan, according to figure 1 The P-f droop ...
PUM
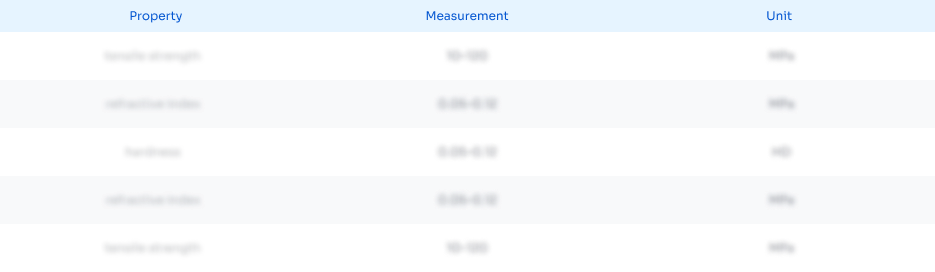
Abstract
Description
Claims
Application Information

- R&D
- Intellectual Property
- Life Sciences
- Materials
- Tech Scout
- Unparalleled Data Quality
- Higher Quality Content
- 60% Fewer Hallucinations
Browse by: Latest US Patents, China's latest patents, Technical Efficacy Thesaurus, Application Domain, Technology Topic, Popular Technical Reports.
© 2025 PatSnap. All rights reserved.Legal|Privacy policy|Modern Slavery Act Transparency Statement|Sitemap|About US| Contact US: help@patsnap.com