High-reliability electromagnetic power-off brake
An electromagnetic power loss and reliability technology, applied in the direction of brake type, axial brake, brake actuator, etc., can solve the problems of small contact surface, failure, poor braking performance of electromagnetic power loss brake, etc., and achieve volume and Small weight, fast response, good braking performance
- Summary
- Abstract
- Description
- Claims
- Application Information
AI Technical Summary
Problems solved by technology
Method used
Image
Examples
Embodiment 1
[0031] Depend on figure 1 , figure 2 , image 3 , Figure 4 and Figure 5 As shown, the iron core 1 is provided with an annular groove 3 for accommodating the coil winding 2, the iron core 1 is provided with a plurality of spring grooves 5 for accommodating the compression spring 4, the coil winding 2 is arranged in the annular groove 3, and the compression spring One end of 4 is embedded in the spring groove 5 of the iron core. The cover plate 6 and the iron core 1 are fixed to each other. The space is fixed by screws 8, and the screws 8 are screwed with the iron core 1 after the cover plate 6 passes through the contour column 7.
[0032] The armature 9 is interposed between the iron core 1 and the cover plate 6, the armature 9 has a through hole 10 matched with the outer diameter of the contour column 7 and is slidably connected between the iron core 1 and the cover plate 6, the other end of the compression spring 4 is connected to the One end face of the armature 9 is...
Embodiment 2
[0037] like Image 6As shown, the iron core 1 is provided with an annular groove 3 for accommodating the coil winding 2, the iron core 1 is provided with a plurality of spring grooves 5 for accommodating the compression spring 4, the coil winding 2 is arranged in the annular groove 3, and the compression spring One end of 4 is embedded in the spring groove 5 of the iron core. The cover plate 6 and the iron core 1 are fixed to each other. The space is fixed by screws 8, and the screws 8 are screwed with the iron core 1 after the cover plate 6 passes through the contour column 7.
[0038] The armature 9 is interposed between the iron core 1 and the cover plate 6, the armature 9 has a through hole 10 matched with the outer diameter of the contour column 7 and is slidably connected between the iron core 1 and the cover plate 6, the other end of the compression spring 4 is connected to the One end face of the armature 9 is offset; the brake disc 11 is interposed between the armatu...
PUM
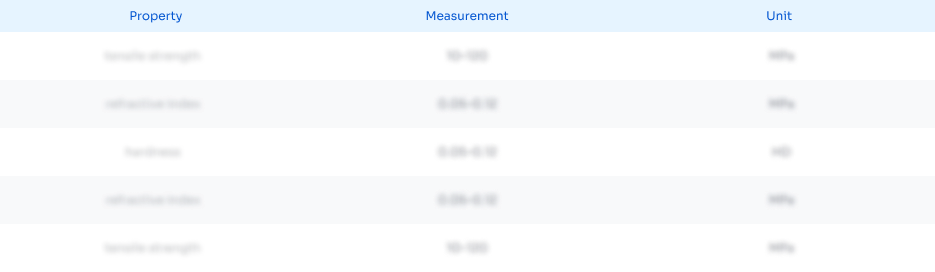
Abstract
Description
Claims
Application Information

- R&D Engineer
- R&D Manager
- IP Professional
- Industry Leading Data Capabilities
- Powerful AI technology
- Patent DNA Extraction
Browse by: Latest US Patents, China's latest patents, Technical Efficacy Thesaurus, Application Domain, Technology Topic, Popular Technical Reports.
© 2024 PatSnap. All rights reserved.Legal|Privacy policy|Modern Slavery Act Transparency Statement|Sitemap|About US| Contact US: help@patsnap.com