A composite insulator manufacturing process
A manufacturing process and insulator technology, applied in the field of composite insulator manufacturing process, can solve the problems of tearing of silicone rubber sheds, poor flow performance, and difficulty in demoulding, and achieve the effect of reducing difficulty and accelerating separation speed.
- Summary
- Abstract
- Description
- Claims
- Application Information
AI Technical Summary
Problems solved by technology
Method used
Image
Examples
Embodiment Construction
[0036] The embodiments of the present invention will be described in detail below with reference to the accompanying drawings, but the present invention can be implemented in many different ways defined and covered by the claims.
[0037] Such as Figure 1 to Figure 7 As shown, a composite insulator manufacturing process uses an injection molding mold. The injection molding mold includes a base frame 1, an installation frame 2, an upper mold 3, a lower mold 4, a lifting cylinder 5 and a vibration mechanism 6. The specific process flow of the composite insulator made by the above injection molding mold is as follows:
[0038] S1. Mandrel molding: After impregnating the glass fiber with epoxy resin, the mandrel is obtained by vacuum injection, continuous pultrusion and curing;
[0039] S2. Mandrel grinding: Grinding the surface of the mandrel to increase the contact area between the surface and the rubber material and improve the bonding performance;
[0040] S3. Injection assem...
PUM
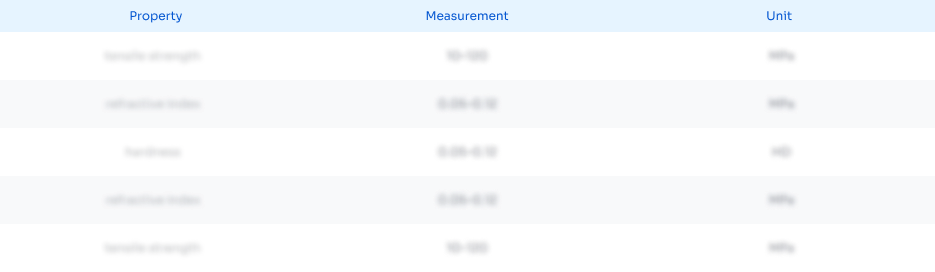
Abstract
Description
Claims
Application Information

- R&D
- Intellectual Property
- Life Sciences
- Materials
- Tech Scout
- Unparalleled Data Quality
- Higher Quality Content
- 60% Fewer Hallucinations
Browse by: Latest US Patents, China's latest patents, Technical Efficacy Thesaurus, Application Domain, Technology Topic, Popular Technical Reports.
© 2025 PatSnap. All rights reserved.Legal|Privacy policy|Modern Slavery Act Transparency Statement|Sitemap|About US| Contact US: help@patsnap.com