Method for establishing PEEK composite material fiber laying heat transfer model
A composite material fiber and transfer model technology, applied in special data processing applications, instruments, electrical digital data processing, etc., can solve problems such as difficulty in accurately reflecting temperature field changes, and achieve good prediction results
- Summary
- Abstract
- Description
- Claims
- Application Information
AI Technical Summary
Problems solved by technology
Method used
Image
Examples
Embodiment Construction
[0017] In order to understand the characteristics and technical content of the present invention in more detail, the implementation of the present invention will be described in detail below in conjunction with the accompanying drawings. The attached drawings are only for reference and description, and are not intended to limit the present invention.
[0018] figure 1 A schematic diagram of the control unit of the two-dimensional model of the thermoplastic fiber filament provided by the embodiment of the present invention; in the figure: heat will be transferred from one unit to its adjacent upper, lower, left, and right units, and point M in the figure represents the middle unit body, such as the dotted line As shown, point L represents the left unit of the middle unit body, point R represents the right unit of the middle unit body, point U represents the upper unit of the middle unit body, and point D represents the lower unit of the middle unit body.
[0019] figure 2 A s...
PUM
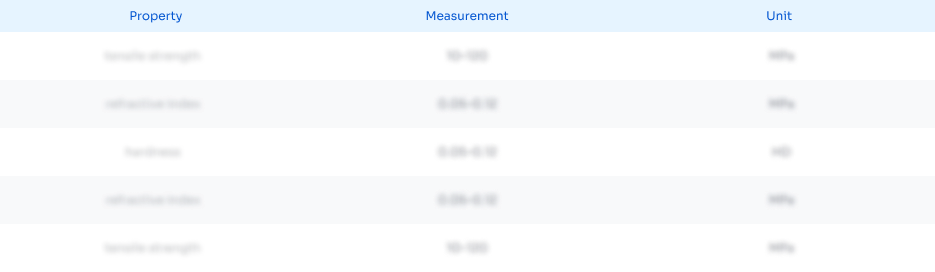
Abstract
Description
Claims
Application Information

- Generate Ideas
- Intellectual Property
- Life Sciences
- Materials
- Tech Scout
- Unparalleled Data Quality
- Higher Quality Content
- 60% Fewer Hallucinations
Browse by: Latest US Patents, China's latest patents, Technical Efficacy Thesaurus, Application Domain, Technology Topic, Popular Technical Reports.
© 2025 PatSnap. All rights reserved.Legal|Privacy policy|Modern Slavery Act Transparency Statement|Sitemap|About US| Contact US: help@patsnap.com