Dry pressing method and equipment for ceramic part forming
A technology of ceramic parts and dry pressing, which is applied in the field of dry pressing methods and equipment for forming ceramic parts, which can solve the problems of unqualified products, large particle gaps, poor compactness, etc., and achieve the effect of improving compactness and smooth extrusion
- Summary
- Abstract
- Description
- Claims
- Application Information
AI Technical Summary
Problems solved by technology
Method used
Image
Examples
Embodiment Construction
[0031] The technical solutions of the present invention will be clearly and completely described below in conjunction with the embodiments. Apparently, the described embodiments are only some of the embodiments of the present invention, not all of them. Based on the embodiments of the present invention, all other embodiments obtained by persons of ordinary skill in the art without creative efforts fall within the protection scope of the present invention.
[0032] Such as Figure 1-5 Shown, a kind of dry pressing method of ceramic part molding, comprises the following steps:
[0033] S1: Filler, add part of the material powder for making the ceramic green body into the lower mold 6;
[0034] S2: pre-compression, pressurization cylinder 91 works, under the cooperation of pressure rod 92, the upper mold 5 is pushed down, the lower mold 6 is stationary, and the powder density at the lower part of the lower mold 6 is increased;
[0035] S3: Secondary filler, add the remaining ma...
PUM
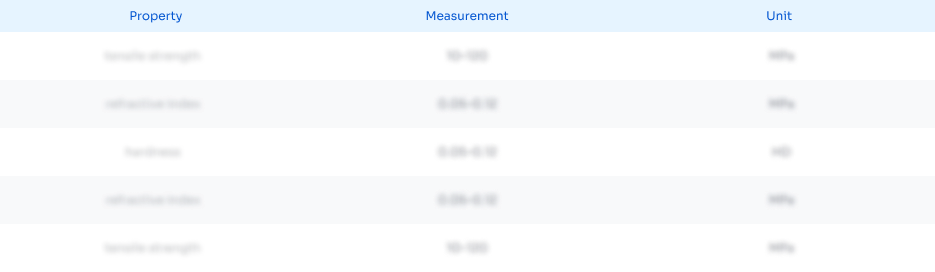
Abstract
Description
Claims
Application Information

- R&D
- Intellectual Property
- Life Sciences
- Materials
- Tech Scout
- Unparalleled Data Quality
- Higher Quality Content
- 60% Fewer Hallucinations
Browse by: Latest US Patents, China's latest patents, Technical Efficacy Thesaurus, Application Domain, Technology Topic, Popular Technical Reports.
© 2025 PatSnap. All rights reserved.Legal|Privacy policy|Modern Slavery Act Transparency Statement|Sitemap|About US| Contact US: help@patsnap.com