Constrained high-speed dynamic balance mechanical calculation method
A high-speed dynamic balance and mechanics technology, applied in the field of dynamic balance mechanics solution, can solve the problems such as failure to effectively ensure whether the intensity value meets the requirements, the implementation process is heavy, and the overall energy of the system is reduced, so as to achieve both operability and ease of use performance, improve dynamic balance accuracy, and ensure smooth operation.
- Summary
- Abstract
- Description
- Claims
- Application Information
AI Technical Summary
Problems solved by technology
Method used
Image
Examples
Embodiment
[0062] figure 1 Shown is that the model is the axial flow compressor rotor of AV50, and it is used as the embodiment object of the present invention, and the parameters needed in the dynamic balance include:
[0063] The number of correction surfaces: This type of rotor has full-circle balance slots reserved on both sides of the shaft section during production and processing, and a screw hole is reserved in the middle of the shaft end for installation of balance weights. Therefore, the number of correction surfaces that can be used is Three, such as figure 1 #1, #2, and #3 respectively represent the three surfaces that can be corrected;
[0064] The number of measuring points: Use the 50-ton high-speed balancing machine produced by Shenke Company for dynamic balancing. At present, there are only two supporting pendulums at the measuring points, so the number of measuring points is two;
[0065] Calibration speed: The dynamic balancing process uses speed up and down, and the ...
PUM
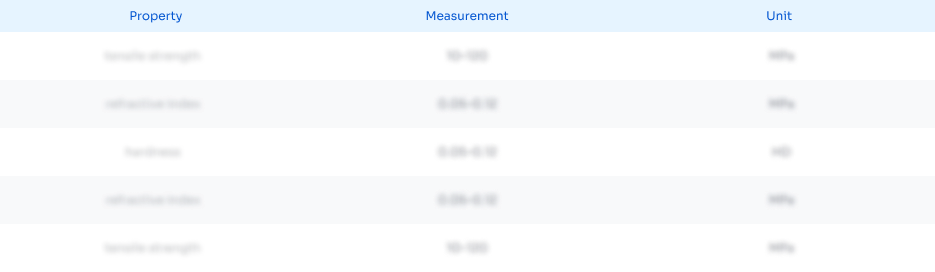
Abstract
Description
Claims
Application Information

- R&D
- Intellectual Property
- Life Sciences
- Materials
- Tech Scout
- Unparalleled Data Quality
- Higher Quality Content
- 60% Fewer Hallucinations
Browse by: Latest US Patents, China's latest patents, Technical Efficacy Thesaurus, Application Domain, Technology Topic, Popular Technical Reports.
© 2025 PatSnap. All rights reserved.Legal|Privacy policy|Modern Slavery Act Transparency Statement|Sitemap|About US| Contact US: help@patsnap.com