Method for reducing content of organic matters in TCPP production wastewater
A technology for the production of wastewater and organic matter, applied in the direction of separation methods, water pollutants, chemical instruments and methods, etc., can solve the problems of complex process, increase of water treatment cost, increase of drug dosage, etc., achieve simple and convenient process, reduce difficulty, and effect significant effect
- Summary
- Abstract
- Description
- Claims
- Application Information
AI Technical Summary
Problems solved by technology
Method used
Image
Examples
Embodiment 1
[0030] Put 1t of solvent xylene and 3t of waste water produced by phosphorus-based flame retardant TCPP into the reaction kettle, stir for 3 hours at a temperature of 40-45°C, and control the stirring speed at 250r / min. After the stirring was completed, the temperature was lowered to below 30° C., and the mixture was allowed to stand for 10 hours, separated into layers, and the lower aqueous phase and the upper organic phase were treated separately.
[0031] The upper organic phase is recycled. The specific method is: put the organic phase into the recovery kettle, raise the temperature and stir, keep the temperature at 100-110°C, and distill under reduced pressure at a vacuum of -0.095--0.1MPa to recover 996kg of solvent by distillation. The rate is 99.6%, and the solvent is recycled after recovery. The recovered organic matter was 14.7kg, accounting for 4.9‰ in the wastewater, and entered the washing step of the next batch of TCPP as a crude product.
[0032] The lower aque...
Embodiment 2
[0034] Put 500kg of solvent xylene and 2t of waste water from the production of phosphorus-based flame retardant TCPP into the reaction kettle, stir for 4 hours at a temperature of 45-50°C, and control the stirring speed to 400r / min. After the stirring was completed, the temperature was lowered to below 30° C., and the mixture was left to stand for 12 hours to separate layers, and the lower aqueous phase and the upper organic phase were treated separately.
[0035] The upper organic phase is recycled. The specific method is: put the organic phase into the recovery kettle, heat up and stir, keep the temperature at 100-110°C, and distill under reduced pressure at a vacuum of -0.095--0.1MPa to recover 493kg of solvent by distillation. The rate is 98.6%, and the solvent is recycled after recovery. 10.3kg of organic matter remained in the recovery kettle, accounting for 5.15‰ in the waste water, and entered the washing process of TCPP as a crude product.
[0036] The lower aqueous...
Embodiment 3
[0038] Put 400kg of solvent toluene and 2t of phosphorus-based flame retardant TCPP production wastewater into the reaction kettle, stir for 5 hours at a temperature of 60-65°C, and control the stirring speed to 400r / min. After the stirring was completed, the temperature was lowered to below 30° C., and the mixture was left to stand for 15 hours to separate layers, and the lower aqueous phase and the upper organic phase were treated separately.
[0039] The upper organic phase is recycled. The specific method is: put the organic phase into the recovery kettle, heat up and stir, keep the temperature at 100-110°C, and distill under reduced pressure at a vacuum of -0.095--0.1MPa to recover 395kg of solvent by distillation. The recovery rate is 98.75%, and the solvent is recycled after recovery. The residual organic matter in the recovery kettle is 9.9kg, accounting for 4.95‰ in the wastewater. The recovered crude product enters the washing process of TCPP.
[0040] The lower aque...
PUM
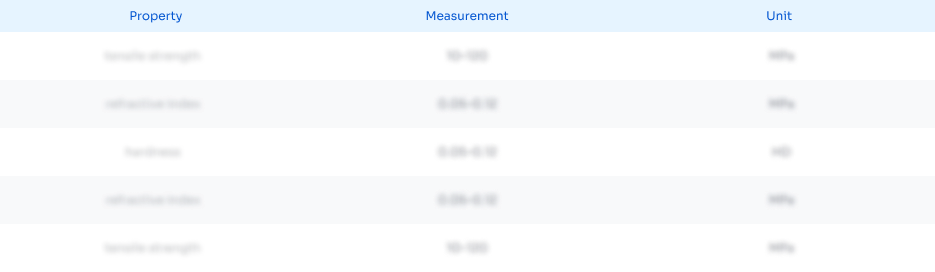
Abstract
Description
Claims
Application Information

- Generate Ideas
- Intellectual Property
- Life Sciences
- Materials
- Tech Scout
- Unparalleled Data Quality
- Higher Quality Content
- 60% Fewer Hallucinations
Browse by: Latest US Patents, China's latest patents, Technical Efficacy Thesaurus, Application Domain, Technology Topic, Popular Technical Reports.
© 2025 PatSnap. All rights reserved.Legal|Privacy policy|Modern Slavery Act Transparency Statement|Sitemap|About US| Contact US: help@patsnap.com