A kind of organosilicon defoamer and preparation method thereof
A silicone defoamer and dispersant technology, applied in the field of defoamer, can solve the problems of layering, affecting product quality, demulsification, etc., achieving excellent water dispersibility, improving centrifugal stability, and improving defoaming performance. Effect
- Summary
- Abstract
- Description
- Claims
- Application Information
AI Technical Summary
Problems solved by technology
Method used
Image
Examples
Embodiment 1
[0041] A silicone defoamer provided in this example comprises the following components in parts by mass: 20 parts of polyether-modified polydimethylsiloxane, 12 parts of polyether, 5 parts of composite emulsifier, dispersion 1.5 parts of food additives, 0.1 parts of food additives, 1.5 parts of stabilizers;
[0042] Wherein, the composite emulsifier is a mixture of Tween-60 and Span-80, wherein the content of Span-80 is 65%, and the content of Tween-60 is 35%;
[0043] The dispersant is non-ionic polyoxyethylene surfactant; the food additive is tert-butyl hydroquinone; the stabilizer is sodium carboxymethyl cellulose.
[0044] The preparation method comprises the following steps:
[0045] (1) To prepare allyl polyether, mix the catalyst potassium hydroxide with allyl alcohol, the mass ratio of potassium hydroxide to allyl alcohol is 1:9, add propylene oxide, and react in vacuum at 120°C. After the reaction is complete, Add ethylene oxide, react in vacuum at 120°C, cool and d...
Embodiment 2
[0056] A silicone defoamer provided in this example comprises the following components in parts by mass: polyether-modified polydimethylsiloxane, 12 parts of polyether, 5 parts of composite emulsifier, 1.5 parts of dispersant 0.1 part of food additive, 1.5 part of stabilizer;
[0057] Wherein, the composite emulsifier is a mixture of Tween-60 and Span-80, wherein the content of Span-80 is 65%, and the content of Tween-60 is 35%;
[0058] The dispersant is non-ionic polyoxyethylene surfactant; the food additive is tert-butyl hydroquinone; the stabilizer is sodium carboxymethyl cellulose.
[0059] The preparation method comprises the following steps:
[0060] (1) To prepare allyl polyether, mix the catalyst potassium hydroxide with allyl alcohol, the mass ratio of potassium hydroxide to allyl alcohol is 1:9, add propylene oxide, and react in a vacuum at 120°C. After the reaction is complete, Add ethylene oxide, wherein the molar ratio of ethylene oxide to propylene oxide is 1:...
Embodiment 3
[0070] A silicone defoamer provided in this example comprises the following components in parts by mass: 20 parts of polyether-modified polydimethylsiloxane, 12 parts of polyether, 5 parts of composite emulsifier, dispersion 1.5 parts of food additives, 0.1 parts of food additives, 1.5 parts of stabilizers;
[0071] Wherein, compound emulsifier is the mixture of Tween-60 and Span-80;
[0072] The dispersant is non-ionic polyoxyethylene surfactant; the food additive is tert-butyl hydroquinone; the stabilizer is sodium carboxymethyl cellulose.
[0073] The preparation method comprises the following steps:
[0074] (1) To prepare allyl polyether, mix the catalyst potassium hydroxide with allyl alcohol, the mass ratio of potassium hydroxide to allyl alcohol is 1:9, add propylene oxide, and react in a vacuum at 120°C. After the reaction is complete, Add ethylene oxide, wherein the molar ratio of ethylene oxide to propylene oxide is 1:4, react in a vacuum at 120°C, cool and discha...
PUM
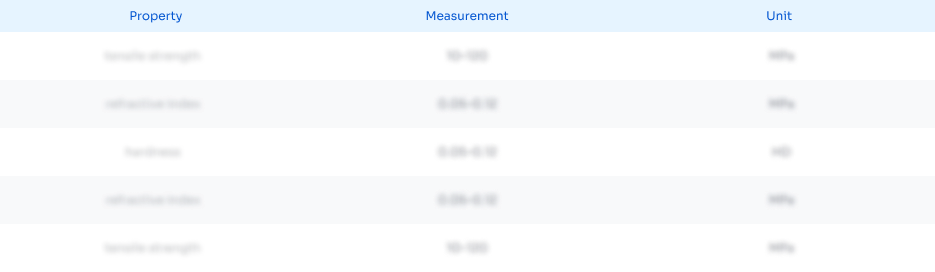
Abstract
Description
Claims
Application Information

- R&D
- Intellectual Property
- Life Sciences
- Materials
- Tech Scout
- Unparalleled Data Quality
- Higher Quality Content
- 60% Fewer Hallucinations
Browse by: Latest US Patents, China's latest patents, Technical Efficacy Thesaurus, Application Domain, Technology Topic, Popular Technical Reports.
© 2025 PatSnap. All rights reserved.Legal|Privacy policy|Modern Slavery Act Transparency Statement|Sitemap|About US| Contact US: help@patsnap.com