Method for smelting austenitic stainless steel by blowing carbon dioxide in AOD converter
A technology of austenitic stainless steel and converter, which is applied in the manufacture of converters, etc. It can solve the problems of high steelmaking cost and low utilization rate of carbon dioxide resources, so as to avoid the pollution of molten steel, reduce the absolute amount, and increase the yield of iron element rate effect
- Summary
- Abstract
- Description
- Claims
- Application Information
AI Technical Summary
Problems solved by technology
Method used
Examples
Embodiment 1
[0023] Smelting steel type: 304 austenitic stainless steel, the smelting steps are as follows:
[0024] a. Add molten iron: inject 90t molten iron with a melting temperature of 1450°C into the AOD converter. The chemical composition of the molten iron is C 2.00%, Si 0.40%, Mn 0.10%, P 0.043%, S 0.10 in terms of mass percentage %, Cr 9.0%, Ni 8.00%, the rest is Fe and unavoidable impurities;
[0025] b. Decarburization: lime is added in the decarburization stage, and the total amount of lime added is 10kg / t steel;
[0026] ①Silicon-aluminum oxidation period: the oxygen flow rate of the top gun is 100Nm 3 / min, side gun oxygen flow rate 100Nm 3 / min, nitrogen flow 30Nm 3 / min, the blowing time is 2min, the amount of light-burned dolomite added is 2kg / t of steel, and 180kg of light-burned dolomite is added;
[0027] ②Main decarburization period: top gun oxygen flow rate 100Nm 3 / min, side gun oxygen flow rate 100Nm 3 / min, nitrogen flow 30Nm 3 / min, blowing time is 2min; ...
Embodiment 2
[0036] Smelting steel type: 304 austenitic stainless steel, the smelting steps are as follows:
[0037] a. Add molten iron: inject 95t molten iron with a melting temperature of 1500°C into the AOD converter. The chemical composition of the molten iron is C 2.50%, Si 0.70%, Mn 0.20%, P 0.040%, S 0.08 in terms of mass percentage %, Cr 8.0%, Ni 8.30%, the rest is Fe and unavoidable impurities;
[0038] b. Decarburization: Lime is added in the decarburization stage, and the total amount of lime added is 12kg / t steel;
[0039] ①Silicon-aluminum oxidation period: the oxygen flow rate of the top gun is 120Nm 3 / min, side gun oxygen flow rate 110Nm 3 / min, nitrogen flow 40Nm 3 / min, the blowing time is 3min, the amount of light-burned dolomite added is 3kg / t steel, and 285kg of light-burned dolomite is added;
[0040] ②Main decarburization period: top gun oxygen flow rate 120Nm 3 / min, side gun oxygen flow rate 110Nm 3 / min, nitrogen flow 40Nm 3 / min, blowing time is 3min;
[...
Embodiment 3
[0049] Smelting steel type: 304 austenitic stainless steel, the smelting steps are as follows:
[0050] a. Add molten iron: inject 92t molten iron with a melting temperature of 1460°C into the AOD converter. The chemical composition of the molten iron is C 2.2%, Si 0.50%, Mn 0.15%, P 0.035%, S 0.09 in terms of mass percentage %, Cr 8.50%, Ni 8.1%, the rest is Fe and unavoidable impurities;
[0051] b. Decarburization: lime is added in the decarburization stage, and the total amount of lime added is 11kg / t steel;
[0052] ①Silicon-aluminum oxidation period: top gun oxygen flow rate 110Nm 3 / min, side gun oxygen flow rate 105Nm 3 / min, nitrogen flow 35Nm 3 / min, the blowing time is 3.5min, the amount of light-burned dolomite added is 2.4kg / t of steel, and 220.8kg of light-burned dolomite is added;
[0053] ②Main decarburization period: top gun oxygen flow rate 110Nm 3 / min, side gun oxygen flow rate 105Nm 3 / min, nitrogen flow 35Nm 3 / min, blowing time is 2.5min;
[0054...
PUM
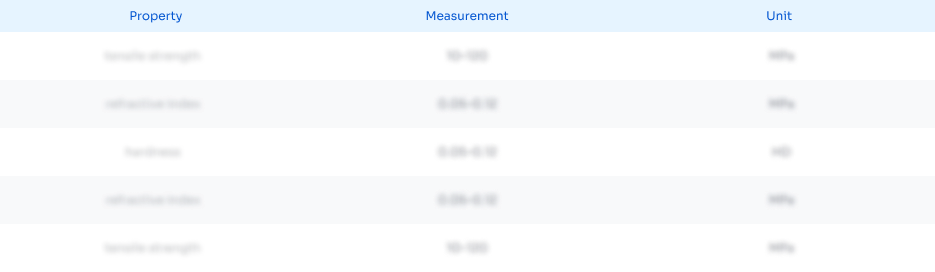
Abstract
Description
Claims
Application Information

- R&D Engineer
- R&D Manager
- IP Professional
- Industry Leading Data Capabilities
- Powerful AI technology
- Patent DNA Extraction
Browse by: Latest US Patents, China's latest patents, Technical Efficacy Thesaurus, Application Domain, Technology Topic, Popular Technical Reports.
© 2024 PatSnap. All rights reserved.Legal|Privacy policy|Modern Slavery Act Transparency Statement|Sitemap|About US| Contact US: help@patsnap.com