Wet-mixed mortar and preparation process
A technology of wet-mixing mortar and preparation technology, which is applied in the field of building materials, can solve the problems of high production cost and low utilization value, and achieve the effect of improving performance, simple steps, and solving the problems of stacking and pollution
- Summary
- Abstract
- Description
- Claims
- Application Information
AI Technical Summary
Problems solved by technology
Method used
Image
Examples
Embodiment 1
[0039] This example provides a kind of wet-mixed mortar, and described wet-mixed mortar comprises the preparation raw material of following parts by weight:
[0040] Modified alkali residue: 5-90 parts,
[0041] Cement: 180-210 parts,
[0042] River sand: 1250~1300 parts,
[0043] Limestone powder: 5-90 parts,
[0044] Water reducer: 2 to 3 parts,
[0045] Water: 210-240 parts.
[0046] Wherein, the water content of the modified alkali slag is 40-50%.
[0047] The preparation method of the modified alkali slag is as follows: adding anhydrous sodium carbonate and water into the alkali slag, stirring and reacting, and suctioning to obtain the product.
[0048] The mass ratio of anhydrous sodium carbonate, water and alkali slag is (11-18): (250-300): (200-220). The stirring reaction time is 0.5-1h. The cement is PO52.5 ordinary Portland cement.
[0049] The water reducer is a polycarboxylate water reducer, and the polycarboxylate water reducer includes PC-50, LDS-850 and ...
Embodiment 2
[0051] This example provides a preparation process of wet-mixed mortar, the process is as follows figure 1 As shown, the steps include:
[0052] S1: Weigh each preparation raw material according to the proportion, add part of the water reducing agent and water into the modified alkali slag and mix evenly to obtain the alkali slag solution;
[0053] S2: mixing cement, river sand and limestone powder to obtain a solid mixture;
[0054] S3: mixing the alkali slag solution in step S1 and the solid mixture in step S2 to obtain a gelled material;
[0055] S4: After adding the remaining water reducer to the cementitious material in step S3 and mixing evenly, pour the slurry into the mold, remove the mold after the first curing at room temperature, and continue the second curing to obtain the wet-mixed mortar.
[0056] Part of the water reducer in step S1 refers to PC-50, and the remaining water reducer in step S4 refers to LDS-10N and LDS-850.
[0057] The time for the first curin...
Embodiment 3
[0059]In this example, a kind of wet-mixed mortar is prepared by adopting the preparation process provided in Example 2, and the preparation raw materials include:
[0060] Modified alkali slag: 5 parts, PO52.5 ordinary portland cement: 210 parts, river sand: 1300 parts, limestone powder: 85.5 parts, water reducing agent: 3 parts, water: 210 parts.
[0061] The mechanical properties and durability of the prepared wet-mixed mortar were tested, and the ordinary wet-mixed mortar was used as a comparison. The results are shown in Table 1 and Table 2.
[0062] The mechanical performance index of the wet-mixed mortar prepared in the embodiment 3 of table 1
[0063]
[0064] The durability performance index of the wet-mixed mortar prepared by the embodiment 3 of table 2
[0065]
PUM
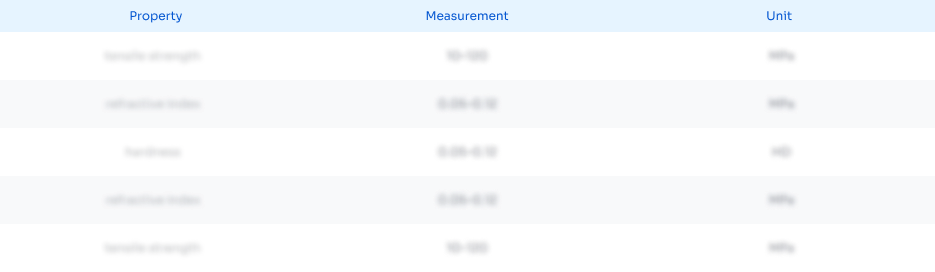
Abstract
Description
Claims
Application Information

- R&D Engineer
- R&D Manager
- IP Professional
- Industry Leading Data Capabilities
- Powerful AI technology
- Patent DNA Extraction
Browse by: Latest US Patents, China's latest patents, Technical Efficacy Thesaurus, Application Domain, Technology Topic, Popular Technical Reports.
© 2024 PatSnap. All rights reserved.Legal|Privacy policy|Modern Slavery Act Transparency Statement|Sitemap|About US| Contact US: help@patsnap.com