High-performance water-resistant antifouling stone-like coating
A high-performance technology of real stone paint, applied in the field of coatings, can solve the problems of peeling off, the surface of real stone paint is easy to be polluted, and reduce the water and antifouling performance and water resistance of real stone paint, so as to achieve the effect of strong antifouling ability and colorful appearance
- Summary
- Abstract
- Description
- Claims
- Application Information
AI Technical Summary
Problems solved by technology
Method used
Examples
Embodiment 1
[0030] High-performance water-resistant and anti-fouling real stone paint, in parts by weight, includes the following components:
[0031] Silicone acrylic emulsion 30 parts
[0032] Natural colored sand 80 parts
[0033] Rock slices 3 servings
[0034] Coalescing aid 0.5 parts
[0035] Thickener 0.1 parts
[0036] Surfactant 0.05 part
[0037] Multi-functional additive 0.1 part
[0038] Antifouling agent 2 parts
[0039] 0.2 parts of defoamer
[0040] Hydrophobic agent 0.2 parts
[0041] 10 parts of water;
[0042] In the film-forming auxiliary agent, the mass ratio of diethylene glycol monobutyl ether to diethyl butyl ether acetate is 1:1;
[0043] Mix the above-mentioned raw materials, stir at room temperature at a speed of 600 rpm for 20 minutes, and mix evenly to obtain the real stone paint coating of the present invention.
[0044] Spray the real stone paint coating of the present invention on the mortar block, the spray pressure is 0.8Pa / cm 2 , the spray gun d...
Embodiment 2
[0051] High-performance water-resistant and anti-fouling real stone paint, in parts by weight, includes the following components:
[0052] Silicone acrylic emulsion 35 parts
[0053] Natural colored sand 100 parts
[0054] Rock slices 4 parts
[0055] Coalescing aid 1 part
[0056] Thickener 0.2 parts
[0057] Surfactant 0.1 parts
[0058] 0.2 parts of multifunctional additive
[0059] Antifouling agent 3 parts
[0060] 0.3 parts of defoamer
[0061] Hydrophobic agent 0.3 part
[0062] 13 parts of water;
[0063] In the film-forming auxiliary agent, the mass ratio of diethylene glycol monobutyl ether to diethyl butyl ether acetate is 1:2;
[0064] Mix the above-mentioned raw materials, stir at room temperature at a speed of 600 rpm for 20 minutes, and mix evenly to obtain the real stone paint coating of the present invention.
[0065] Spray the real stone paint coating of the present invention on the mortar block, the spray pressure is 0.8Pa / cm 2 , the spray gun diam...
Embodiment 3
[0072] High-performance water-resistant and anti-fouling real stone paint, in parts by weight, includes the following components:
[0073] Silicone acrylic emulsion 40 parts
[0074] Natural colored sand 120 parts
[0075] Rock slices 5 parts
[0076] Coalescing aid 1 part
[0077] Thickener 0.2 parts
[0078]Surfactant 0.1 parts
[0079] 0.2 parts of multifunctional additive
[0080] Antifouling agent 3 parts
[0081] 0.3 parts of defoamer
[0082] Hydrophobic agent 0.3 part
[0083] 15 parts of water;
[0084] In the film-forming auxiliary agent, the mass ratio of diethylene glycol monobutyl ether to diethyl butyl ether acetate is 1:1.5;
[0085] Mix the above-mentioned raw materials, stir at room temperature at a speed of 600 rpm for 20 minutes, and mix evenly to obtain the real stone paint coating of the present invention.
[0086] Spray the real stone paint coating of the present invention on the mortar block, and the spraying pressure is at 0.8Pa / cm 2 , the ca...
PUM
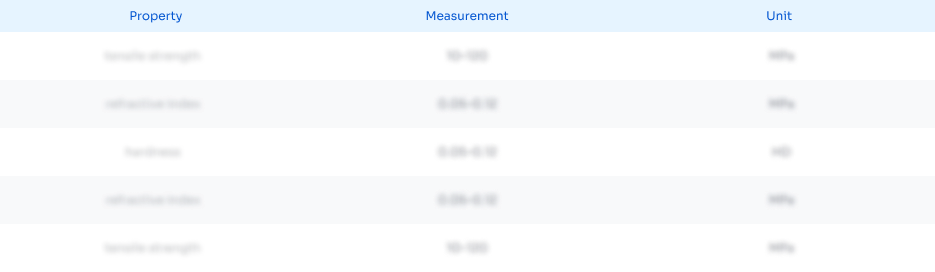
Abstract
Description
Claims
Application Information

- R&D Engineer
- R&D Manager
- IP Professional
- Industry Leading Data Capabilities
- Powerful AI technology
- Patent DNA Extraction
Browse by: Latest US Patents, China's latest patents, Technical Efficacy Thesaurus, Application Domain, Technology Topic, Popular Technical Reports.
© 2024 PatSnap. All rights reserved.Legal|Privacy policy|Modern Slavery Act Transparency Statement|Sitemap|About US| Contact US: help@patsnap.com