Efficient production process of high-standard bearing steel
A standard bearing and production process technology, applied in the manufacture of converters, etc., can solve the problems of reducing the production efficiency of bearing steel, easy transformation of inclusions, and increasing the probability of calcium-aluminate inclusions exceeding the standard, etc.
- Summary
- Abstract
- Description
- Claims
- Application Information
AI Technical Summary
Problems solved by technology
Method used
Image
Examples
Embodiment 1
[0022] Finished steel composition C: 0.96%, Si: 0.22%, Mn: 0.35%, P: 0.011%, S: 0.007%, Al: 0.015%, Cr: 1.47%.
[0023]The converter adopts double slag process, the raw materials are molten iron and scrap steel, and the ratio of scrap steel is 15%. Converter blowing 5min to carry out slagging operation, converter final slag basicity is 3.2, FeO content is 16%, converter end point C content is 0.05%, end point P content is 0.011%, end point S is controlled at 0.007%, converter tapping temperature is 1668°C. Add 140kg of aluminum cake during the tapping process, then add 250kg of preheated low-titanium and low-aluminum ferrosilicon, 400kg of high-carbon ferromanganese, 2800kg of low-titanium and high-carbon ferrochrome, then add 1000kg of low-nitrogen carburizer, and add 600kg of lime and 100kg fluorite for slag making. The temperature of the molten steel after tapping from the converter is 1574°C.
[0024] The composition of the slag entering the RH station is shown in Table...
Embodiment 2
[0033] Finished steel composition C: 0.97%, Si: 0.25%, Mn: 0.32%, P: 0.013%, S: 0.008%, Al: 0.018%, Cr: 1.42%.
[0034] The converter adopts double slag process, the raw materials are molten iron and scrap steel, and the ratio of scrap steel is 15%. Converter blowing 5min to carry out slagging operation, converter final slag basicity is 3.5, FeO content is 14%, converter end point C content is 0.07%, end point P content is 0.013%, end point S is controlled at 0.008%, converter tapping temperature is 1689°C. Add 140kg of aluminum cake during the tapping process, then add 250kg of preheated low-titanium and low-aluminum ferrosilicon, 400kg of high-carbon ferromanganese, 2800kg of low-titanium and high-carbon ferrochrome, then add 1000kg of low-nitrogen carburizer, and add 600kg of lime and 100kg fluorite for slag making. The temperature of the molten steel after tapping from the converter is 1583°C.
[0035] The composition of the slag entering the RH station is shown in Tabl...
PUM
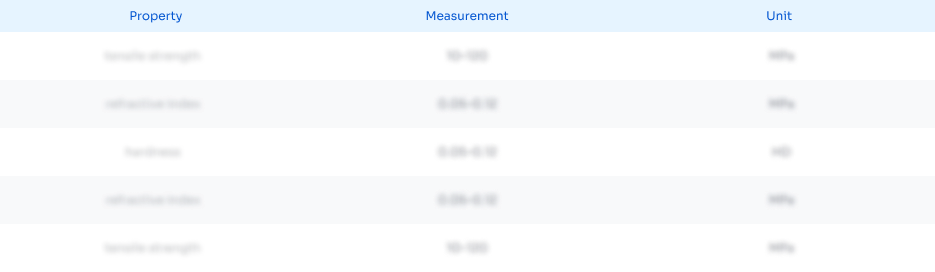
Abstract
Description
Claims
Application Information

- R&D Engineer
- R&D Manager
- IP Professional
- Industry Leading Data Capabilities
- Powerful AI technology
- Patent DNA Extraction
Browse by: Latest US Patents, China's latest patents, Technical Efficacy Thesaurus, Application Domain, Technology Topic, Popular Technical Reports.
© 2024 PatSnap. All rights reserved.Legal|Privacy policy|Modern Slavery Act Transparency Statement|Sitemap|About US| Contact US: help@patsnap.com