Bridge and tunnel intelligent detection vehicle mechanical arm system
A technology of intelligent detection and robotic arm, which is applied in the direction of bridges, bridge parts, bridge construction, etc., can solve the problems of low detection efficiency, inability to detect, high investment cost, etc., and achieve the effect of high rigidity, large torque and good stability
- Summary
- Abstract
- Description
- Claims
- Application Information
AI Technical Summary
Problems solved by technology
Method used
Image
Examples
Embodiment Construction
[0014] Such as Figure 1 ~ Figure 4 As shown, it is an embodiment of the present invention. The bridge and tunnel intelligent detection vehicle mechanical arm system includes a load-carrying vehicle (1), a base (2), a first section mechanical arm (3), a swing drive device A (4), a second section Mechanical arm (5), telescopic drive device A (6), swing drive device B (7), swivel joint (8), telescopic drive device B (9), third-section mechanical arm (10) and detection equipment (11) ; The base (2) is fixed in the compartment of the carrying vehicle (1), its axis is vertical, the first mechanical arm (3) is placed horizontally, and is connected with the base (2) through a bearing support, the first mechanical arm (3) It can rotate in the horizontal plane, and the rotation of the first mechanical arm (3) is driven by a servo motor through a reducer; the second mechanical arm (5) is connected with the first mechanical arm (3) through a hinge, and the second mechanical arm (5) Unde...
PUM
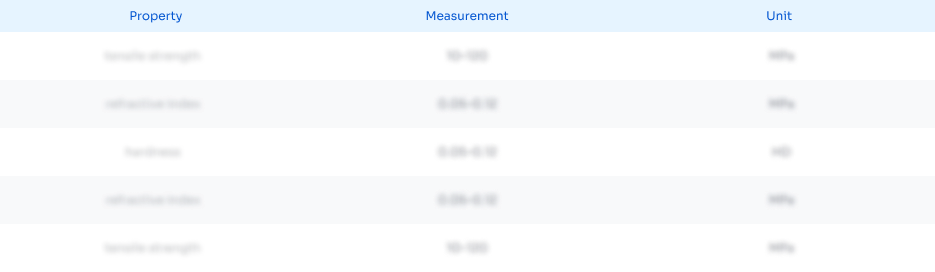
Abstract
Description
Claims
Application Information

- R&D
- Intellectual Property
- Life Sciences
- Materials
- Tech Scout
- Unparalleled Data Quality
- Higher Quality Content
- 60% Fewer Hallucinations
Browse by: Latest US Patents, China's latest patents, Technical Efficacy Thesaurus, Application Domain, Technology Topic, Popular Technical Reports.
© 2025 PatSnap. All rights reserved.Legal|Privacy policy|Modern Slavery Act Transparency Statement|Sitemap|About US| Contact US: help@patsnap.com