Multi-component rare earth magnesium alloy 3D printing process
A 3D printing, rare earth magnesium technology, applied in the field of multi-component rare earth magnesium alloy 3D printing process, can solve the problems of spheroidization, low sample density, large residual stress, etc., achieving high scientific research value and novel alloy types , Reasonable effect of burning loss control
- Summary
- Abstract
- Description
- Claims
- Application Information
AI Technical Summary
Problems solved by technology
Method used
Image
Examples
Example
[0035] Comparative experiment example:
[0036] In the conventional 3D printing process, under normal circumstances, the sample is warped and cracked, which affects the powder coating process. Generally, it occurs when the powder layer thickness reaches 0.5mm. If the above defects do not occur when the height exceeds 0.5mm, the 3D The printing process can proceed normally. But for this alloy, there is no problem when the powder layer thickness reaches 1.5mm, but warpage and cracks occur at 1.6mm ( Figure 4 ), which limits the powder coating process, the powder coating height of 1.6mm is a threshold for the alloy 3D printing process. After the applicant modified the process many times, the process proposed in this application finally solved this problem successfully.
[0037] For conventional magnesium alloy 3D printing, the parameter range span of laser power and scanning speed is generally 120w and 800mm / s, and the selection of power and speed has a large parameter range. ...
PUM
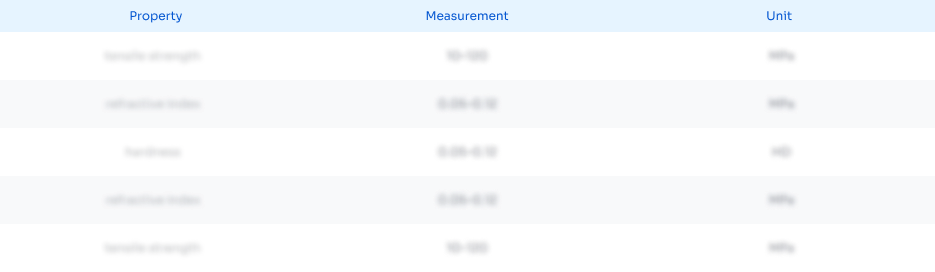
Abstract
Description
Claims
Application Information

- R&D Engineer
- R&D Manager
- IP Professional
- Industry Leading Data Capabilities
- Powerful AI technology
- Patent DNA Extraction
Browse by: Latest US Patents, China's latest patents, Technical Efficacy Thesaurus, Application Domain, Technology Topic, Popular Technical Reports.
© 2024 PatSnap. All rights reserved.Legal|Privacy policy|Modern Slavery Act Transparency Statement|Sitemap|About US| Contact US: help@patsnap.com