Resistance spot welding method and method for manufacturing welded member
A technology of resistance spot welding and welding conditions, which is applied in the direction of resistance welding equipment, welding power supply, manufacturing tools, etc., can solve the problem that the nugget diameter cannot be ensured, and achieve the effect of improving operation efficiency
- Summary
- Abstract
- Description
- Claims
- Application Information
AI Technical Summary
Problems solved by technology
Method used
Image
Examples
Embodiment
[0137] For the plate group of 2 or 3 overlapping metal plates shown in Table 1, test welding is carried out under the conditions shown in Table 1, and then, for the 2 or 3 overlapping metal plates shown in Table 2 The plate group of plates was subjected to main welding under the conditions shown in Table 2 to produce welded joints (welded parts).
[0138] Here, trial soldering and main soldering are performed in such figure 1 with figure 2 The unperturbed state is shown as well as Figure 3-6 The simulations shown were performed under the perturbed state. In the figure, symbols 11, 12 and 13 are metal plates, 14 is an electrode, 15 is a spacer, and 16 is a welded point. It should be stated that in image 3 with Figure 4 Among them, spacers 15 are inserted between the metal plates 11-12 and between the metal plates 12-13, and clamped from above and below (not shown), thereby providing gaps having various gap thicknesses tg. It should be noted that the plate gap distance...
PUM
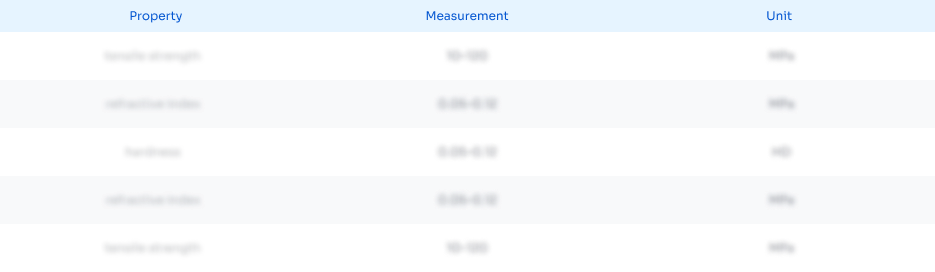
Abstract
Description
Claims
Application Information

- R&D Engineer
- R&D Manager
- IP Professional
- Industry Leading Data Capabilities
- Powerful AI technology
- Patent DNA Extraction
Browse by: Latest US Patents, China's latest patents, Technical Efficacy Thesaurus, Application Domain, Technology Topic, Popular Technical Reports.
© 2024 PatSnap. All rights reserved.Legal|Privacy policy|Modern Slavery Act Transparency Statement|Sitemap|About US| Contact US: help@patsnap.com